π Standards, Codes & Compliance in Oil & Gas β Master Industry Regulations! βοΈ
The oil & gas industry relies on strict standards, codes, and compliance measures to ensure safety, efficiency, and environmental sustainability. Mastering these regulations is essential for engineers, project managers, and safety professionals.
Chemical ( Process)
Instrumentation
Mechanical
Electrical
Civil
CODE
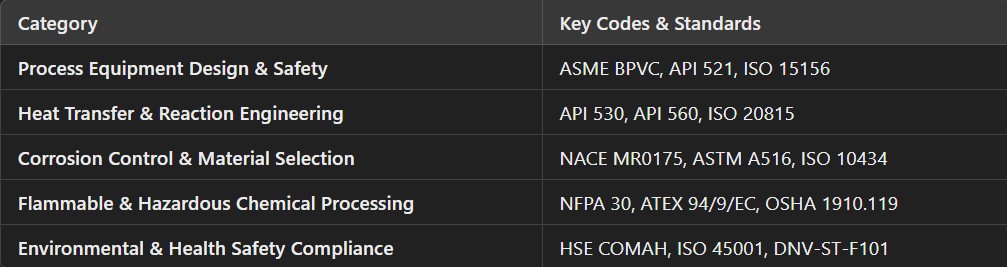
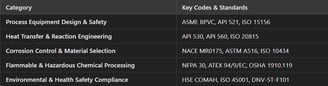
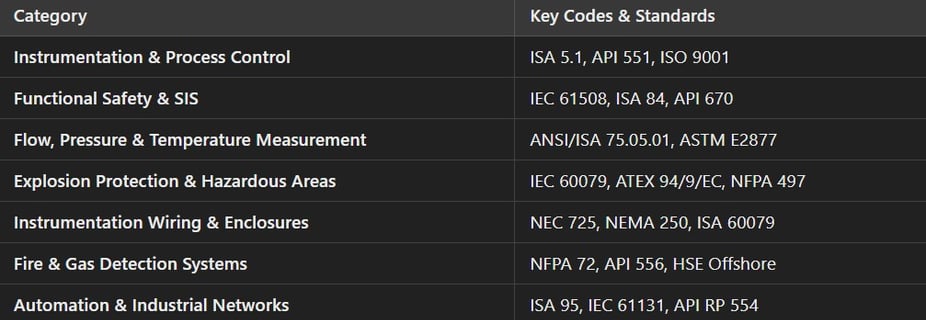
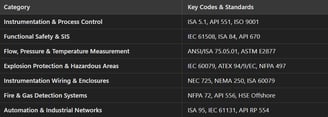
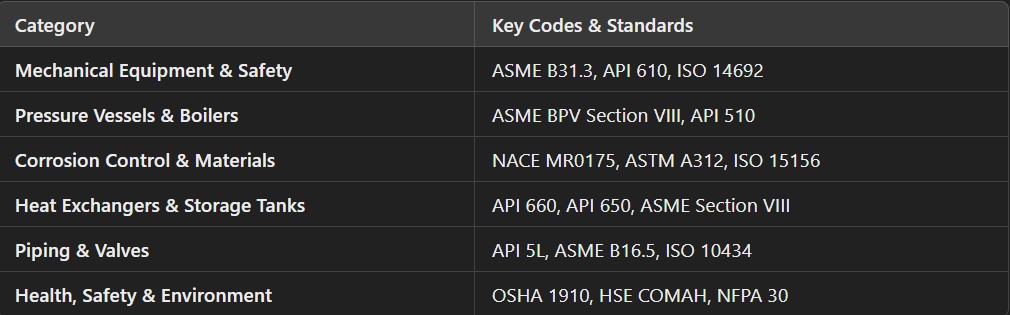
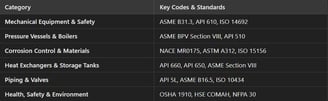
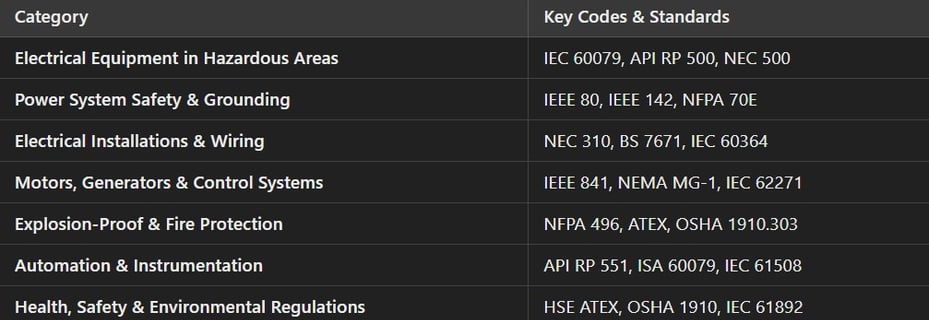
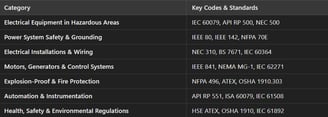
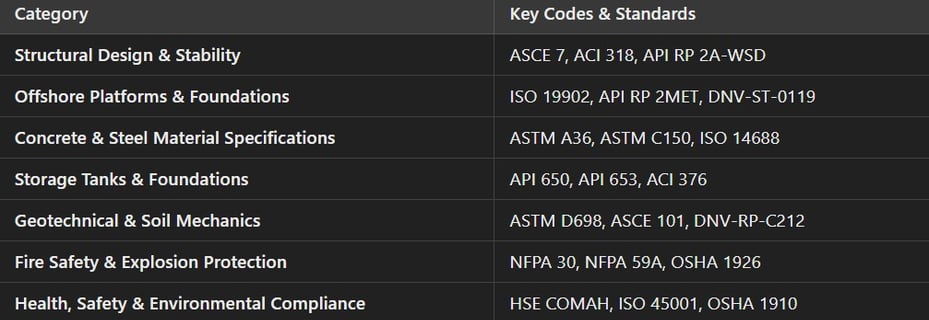
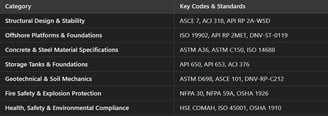
ASME B31.3 & B31.1 Piping Codes β Process & Power Piping Regulations π₯π§
The ASME (American Society of Mechanical Engineers) B31 series is the gold standard for designing, fabricating, testing, and maintaining safe and reliable piping systems. These codes ensure high performance, safety, and regulatory compliance for process and power piping across multiple industries.
β 1. ASME B31.3 β Process Piping Code ππ‘
β ASME B31.3 applies to high-pressure, high-temperature piping systems used in:
πΉ Refineries
πΉ Chemical & petrochemical plants
πΉ Offshore oil & gas platforms
πΉ Pharmaceutical & food processing industries
π Key Features & Requirements of ASME B31.3
1.1 High-Pressure & High-Temperature Piping Design π₯
β Covers piping systems operating under extreme conditions, such as:
β
High-pressure fluid transport (above 15 psi)
β
High-temperature chemical reactions & steam pipelines
β
Cryogenic piping for LNG & industrial gases (-196Β°C)
πΉ Example: Refineries use ASME B31.3-compliant pipes to handle superheated steam, crude oil, and corrosive chemicals at extreme temperatures.
1.2 Stress Analysis & Material Selection β Ensuring Piping Integrity π©
β Process piping experiences thermal expansion, vibration & fluctuating pressures.
β ASME B31.3 mandates stress analysis to prevent:
β
Pipe failures due to excessive thermal stress
β
Material fatigue & corrosion cracking
β
Joint leakage in high-pressure environments
πΉ Example: Offshore platforms use stress-analyzed piping layouts to withstand harsh marine environments & wave-induced vibrations.
1.3 Welding Procedures & Corrosion Prevention β‘π
β High-temperature fluids and chemicals can cause weld failures & pipeline degradation.
β ASME B31.3 requires:
β
Certified welding procedures (WPS, PQR) for pipe joints
β
Non-destructive testing (NDT) of welds to detect cracks & defects
β
Protective coatings & cathodic protection to prevent corrosion
πΉ Example: Chemical plants use corrosion-resistant stainless steel & alloy piping to transport acidic fluids safely.
β 2. ASME B31.1 β Power Piping Code βοΈπ¨
β ASME B31.1 applies to power generation and high-energy fluid transport, including:
πΉ Power plants (coal, nuclear, natural gas, solar)
πΉ Boilers & steam piping systems
πΉ Turbine piping & district heating networks
πΉ Pressure vessels & heat exchangers
π Key Features & Requirements of ASME B31.1
2.1 Governs Steam, Condensate & High-Energy Fluid Transport π‘
β Covers high-pressure steam & hot water piping, essential for power generation.
β Ensures safe transport of superheated fluids & condensate return systems.
πΉ Example: Nuclear power plants follow ASME B31.1 standards for steam turbines & pressurized coolant loops to ensure safety.
2.2 Pipe Support Design, Expansion Control & Safety Relief Systems π
β Power piping systems expand and contract due to extreme heat fluctuations.
β ASME B31.1 mandates:
β
Expansion joints & loops to handle thermal expansion
β
Pipe supports & hangers to prevent sagging and vibration failure
β
Pressure relief valves & safety shutdown systems
πΉ Example: Boilers in power plants use spring hangers & sliding supports to allow movement without damaging the pipes.
2.3 Preventing Thermal Expansion, Vibration & Fatigue Failures π
β Power piping experiences continuous thermal cycling and dynamic forces.
β ASME B31.1 requires:
β
Fatigue analysis to avoid pipe cracks from temperature fluctuations
β
Vibration dampers & braces to reduce mechanical stress
β
Routine inspections & hydrostatic pressure testing
πΉ Example: Gas-fired power plants use high-strength alloy steel piping to transport superheated steam at 600Β°C+.
π ASME B31.3 vs. ASME B31.1 β Whatβs the Difference?
π The Importance of ASME Piping Codes in Industry
πΉ Ensures pipeline safety & integrity in high-risk environments.
πΉ Prevents catastrophic failures in refineries, power plants & offshore platforms.
πΉ Reduces maintenance costs by enforcing high-quality materials & construction methods.
π ASME B31.3 & B31.1 are critical for ensuring reliable, efficient, and safe piping systems worldwide! π
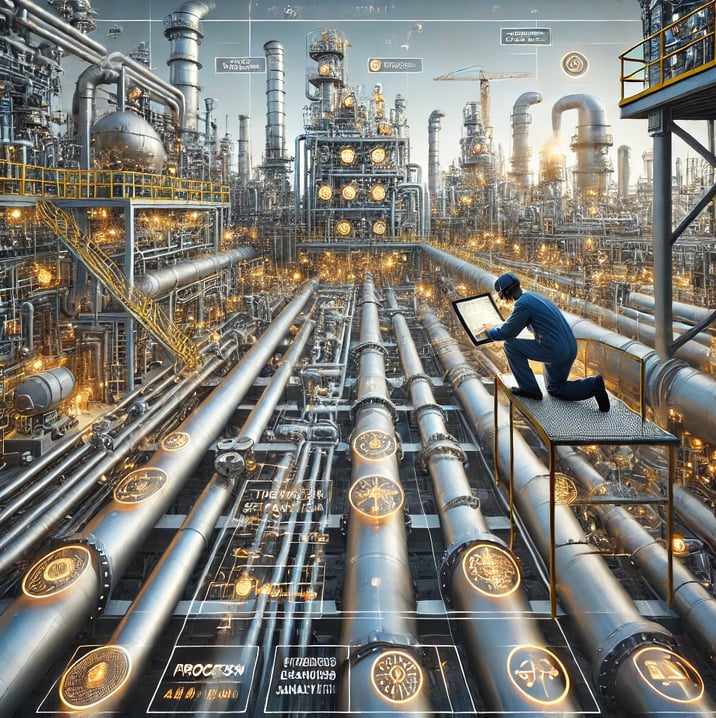
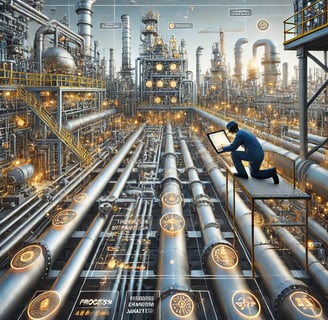
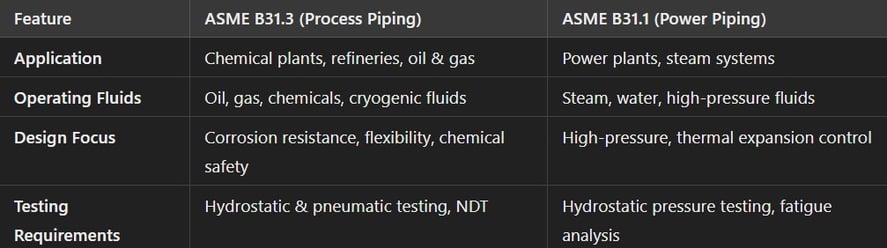
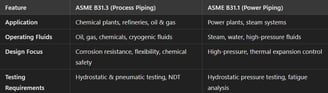
API 570 & API 653 Standards β Inspection & Maintenance Requirements π§π’
The American Petroleum Institute (API) establishes industry-leading inspection and maintenance standards to ensure the safety, reliability, and longevity of oil & gas piping systems and storage tanks. These standards help prevent leaks, corrosion, and catastrophic failures in refineries, terminals, and industrial facilities.
β 1. API 570 β Piping Inspection Code ππ
β API 570 regulates the inspection, repair, and alteration of in-service piping systems in:
πΉ Refineries & petrochemical plants
πΉ Oil terminals & pipelines
πΉ Chemical processing plants
πΉ Power plants with high-pressure steam piping
π Key Features & Requirements of API 570
1.1 Corrosion Monitoring & Pressure Testing β Preventing Pipe Failures π‘
β API 570 requires corrosion monitoring programs to assess pipe wall thinning, erosion, and material degradation.
β Periodic pressure testing ensures piping systems operate within safe pressure limits.
πΉ Common Corrosion Detection Methods:
β
Ultrasonic Thickness Testing (UTT) β Measures pipe wall thinning.
β
Radiographic Testing (RT) β Detects internal cracks & defects.
β
Magnetic Particle Testing (MPT) β Finds surface and near-surface cracks.
πΉ Example: Refineries use UTT & RT to detect thinning in hydrocarbon transport pipes before leaks occur.
1.2 Weld Integrity & NDT (Non-Destructive Testing) Inspections π
β API 570 requires weld quality assessments to prevent failures at pipe joints.
β NDT techniques detect defects without cutting or damaging pipes.
πΉ Types of NDT Inspections:
β
Phased Array Ultrasonic Testing (PAUT) β Advanced crack detection.
β
Eddy Current Testing (ECT) β Identifies material fatigue & stress.
β
Acoustic Emission Testing (AET) β Detects real-time leak sources.
πΉ Example: Crude oil pipelines undergo PAUT scans to check for welding defects.
1.3 Fitness-for-Service (FFS) Assessments β Evaluating Aging Pipes π
β API 570 defines FFS criteria to determine whether aging pipelines can remain in service or need replacement.
β Engineers assess corrosion rates, stress limits, and material properties.
πΉ Example: Old pipelines in refineries undergo FFS assessments to extend service life without costly replacements.
β 2. API 653 β Aboveground Storage Tank (AST) Inspection Standard π’π
β API 653 applies to large aboveground storage tanks (ASTs) used in:
πΉ Oil refineries & fuel storage terminals
πΉ Petrochemical plants & aviation fuel depots
πΉ Bulk liquid storage facilities
π Key Features & Requirements of API 653
2.1 Preventing Tank Leaks, Corrosion & Structural Failures π
β API 653 requires periodic tank inspections to detect corrosion, leakage, and metal fatigue.
β Common corrosion risks in storage tanks:
β
Bottom plate corrosion due to water accumulation.
β
Internal wall thinning from aggressive chemicals.
β
Roof & shell corrosion from moisture and environmental exposure.
πΉ Example: Oil terminals conduct API 653 tank floor scans to prevent leaks into groundwater.
2.2 Hydrostatic Testing & Bottom Plate Evaluations π
β API 653 mandates hydrostatic testing to check tank integrity under full capacity.
β Tank bottom plate evaluations detect leaks & structural weaknesses.
πΉ How Hydrostatic Testing Works:
β
Tanks are filled with water and monitored for leaks.
β
Pressure sensors detect plate deformation & leaks.
β
AI-assisted remote sensors improve test accuracy.
πΉ Example: Jet fuel storage tanks in airports undergo hydrostatic tests to prevent catastrophic failures.
2.3 Compliance with Spill Prevention & Environmental Regulations π±β»
β API 653 aligns with EPAβs Spill Prevention, Control & Countermeasure (SPCC) rules.
β Tank operators must ensure secondary containment to prevent spills.
πΉ Spill Prevention Measures in API 653:
β
Double-walled tanks with leak detection sensors.
β
Dike barriers to contain oil in case of rupture.
β
Real-time tank level monitoring to detect overfills.
πΉ Example: Oil companies install automated tank overflow shutoff valves to comply with API 653 & SPCC regulations.
π API 570 vs. API 653 β Whatβs the Difference?
π Why API 570 & API 653 Matter for Industrial Safety
πΉ Prevents leaks, explosions & environmental disasters in refineries & storage facilities.
πΉ Reduces maintenance costs by ensuring proactive inspections.
πΉ Enhances safety & compliance with global oil & gas regulations.
π API 570 & API 653 are crucial for protecting industrial assets and ensuring safe operations! π
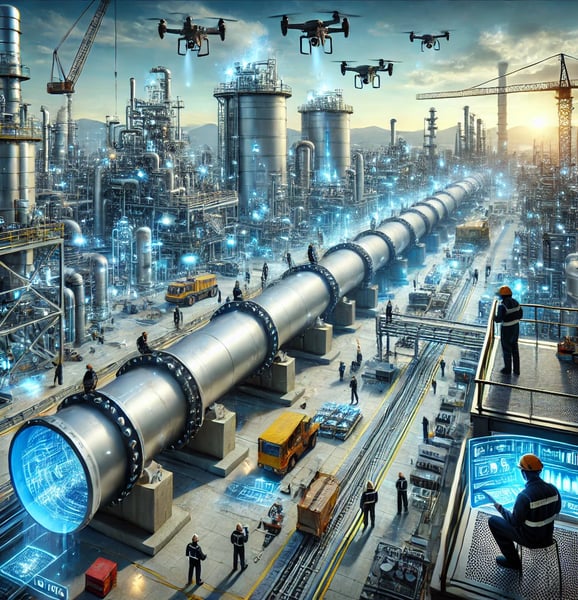
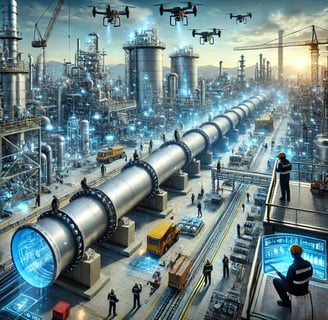
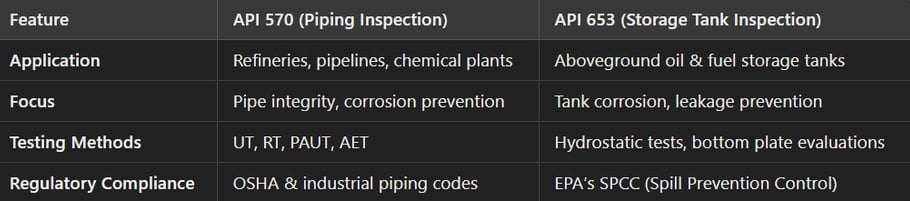
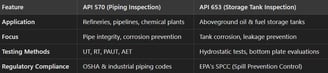
ISO & ASTM Standards for Piping β International Quality Guidelines ππ©
ISO (International Organization for Standardization) and ASTM (American Society for Testing & Materials) define global quality benchmarks for piping materials, fabrication, and design. These standards ensure safety, durability, and compliance in industries such as oil & gas, power plants, refineries, and offshore platforms.
β 1. ISO 9001 β Quality Management System for Piping Fabrication ππ
β ISO 9001 ensures consistent quality control in piping systems, covering:
πΉ Fabrication & welding processes
πΉ Material testing & inspections
πΉ Documentation & compliance reporting
π Key Features of ISO 9001 in Piping Systems
1.1 Consistent Quality Control in Pipe Manufacturing π
β Standardized inspection procedures ensure each pipe meets quality requirements.
β Quality checks include:
β
Dimensional accuracy verification
β
Material composition analysis
β
Hydrostatic pressure testing
πΉ Example: Refinery pipelines undergo ISO 9001-certified testing to ensure leak-proof performance under high pressure.
1.2 Documented Procedures for Design, Testing & Inspections π
β ISO 9001 requires detailed documentation for:
β
Pipe stress analysis & fatigue testing
β
Welding procedure qualification records (WPQR)
β
Non-destructive testing (NDT) records
πΉ Example: Offshore pipelines use ISO 9001-certified welding to ensure integrity in deepwater environments.
β 2. ISO 14692 β Glass-Reinforced Plastic (GRP) Piping Standard ππ¬
β ISO 14692 regulates composite piping materials, used in:
πΉ Chemical & petrochemical plants
πΉ Offshore oil platforms
πΉ Seawater desalination & cooling systems
π Key Features of ISO 14692 in Piping
2.1 Corrosion-Resistant Composite Materials for Harsh Environments π
β GRP pipes are lightweight, durable, and immune to rust & corrosion.
β Used for seawater pipelines & corrosive chemical transport.
πΉ Example: Offshore platforms use GRP piping to prevent seawater corrosion in firewater systems.
2.2 High-Strength, Low-Maintenance Piping Solution π©
β GRP pipes require fewer inspections & repairs compared to steel.
β Reduces long-term maintenance costs by 50%.
πΉ Example: Nuclear power plants use GRP piping for cooling water transport.
β 3. ASTM A106 & A53 β Carbon Steel Pipe Specifications πβοΈ
β ASTM A106 & A53 set industry standards for carbon steel pipes, used in:
πΉ Oil & gas pipelines
πΉ Power plants & steam lines
πΉ Structural piping applications
π Key Features of ASTM A106 & A53
3.1 Chemical Composition, Tensile Strength & Pressure Limits π¬
β ASTM A106 covers seamless high-temperature pipes, while ASTM A53 includes welded & seamless pipes.
β Ensures high-pressure resistance & mechanical durability.
πΉ Example: Gas pipelines in refineries use ASTM A106 carbon steel for superheated steam transport.
3.2 Applications in Industrial Facilities & Oil & Gas Pipelines π’
β ASTM A53 pipes are used for lower-pressure applications, such as:
β
Structural supports in buildings & bridges
β
Water pipelines in municipal systems
πΉ Example: ASTM A53 galvanized pipes are used in fire protection sprinkler systems.
β 4. ISO 15156 (NACE MR0175) β Sour Gas Service Standard β π¨
β ISO 15156 (also known as NACE MR0175) regulates pipelines exposed to sour gas (HβS).
β Applies to:
πΉ Offshore drilling & oil refining
πΉ Gas processing plants
πΉ Petrochemical facilities
π Key Features of ISO 15156 in Sour Gas Pipelines
4.1 Preventing Sulfide Stress Cracking (SSC) in HβS-Exposed Pipelines π¨
β Sour gas contains hydrogen sulfide (HβS), which weakens steel & causes pipeline failure.
β ISO 15156-compliant materials include:
β
High-strength, corrosion-resistant alloys (CRAs)
β
Nickel-based & stainless steel pipes
πΉ Example: Offshore drilling risers use NACE-certified alloys to prevent sulfide stress cracking.
4.2 Safety Standards for HβS-Containing Environments β
β ISO 15156 mandates rigorous safety inspections & material selection for sour gas transport.
β Reduces risks of pipeline ruptures & hazardous gas leaks.
πΉ Example: Natural gas processing plants follow ISO 15156 to ensure pipeline durability in HβS environments.
π ISO & ASTM Standards Comparison
π Why These Standards Matter for the Industry
πΉ Ensures high-quality, durable piping materials for critical applications.
πΉ Prevents failures in high-risk environments (refineries, offshore, power plants).
πΉ Improves pipeline efficiency, safety, and long-term performance.
π ISO & ASTM standards are essential for safe, high-performance piping systems worldwide! π
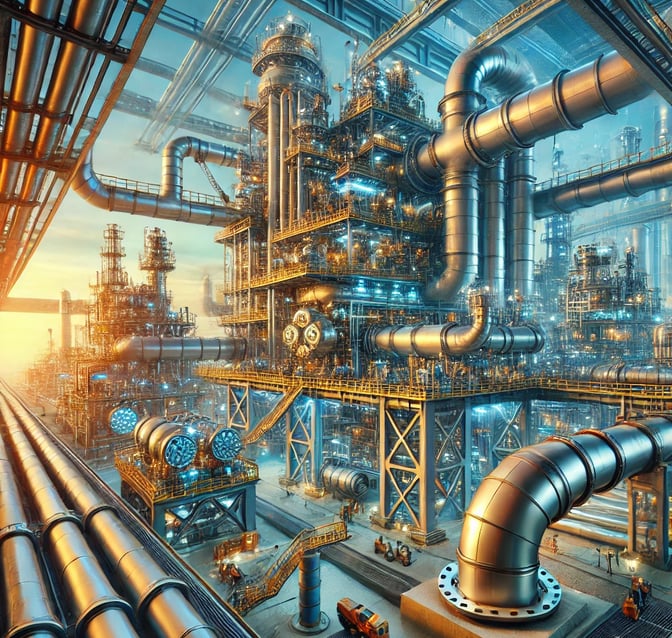
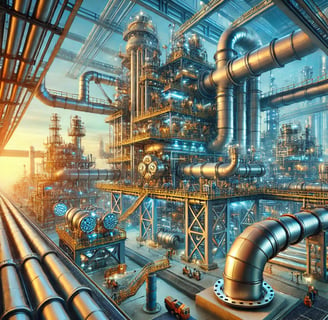
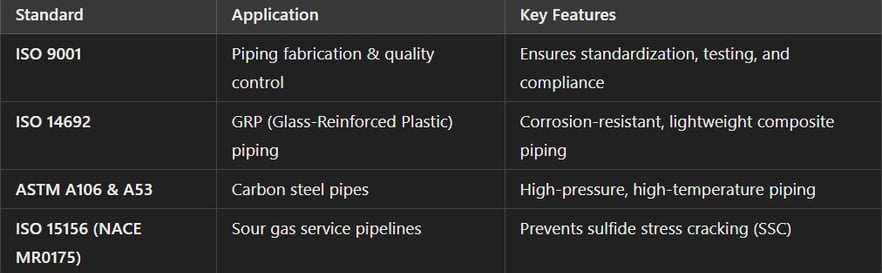
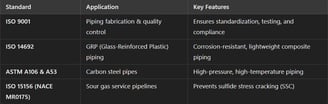
OSHA & HSE Safety Guidelines β Ensuring Workplace Safety β οΈπ₯
Workplace safety is critical in piping, refineries, and oil & gas facilities to prevent accidents, hazardous leaks, fires, and explosions. Compliance with OSHA (Occupational Safety & Health Administration) and HSE (Health, Safety & Environment) regulations helps protect workers, equipment, and the environment.
β 1. OSHA (Occupational Safety & Health Administration) Regulations ππ
β OSHA enforces strict safety standards for oil & gas facilities, refineries, and pipeline operations.
β Key safety regulations include:
π 1.1 Fall Protection, Confined Space Permits & PPE Compliance π¦Ίπ
β Oil & gas workers often work at heights or inside confined spaces (e.g., tanks & pipelines).
β OSHA mandates:
β
Fall protection systems (harnesses, guardrails, scaffolds).
β
Confined space permits & atmospheric testing before entry.
β
Mandatory PPE (Personal Protective Equipment), including flame-resistant clothing, helmets, gloves & gas detectors.
πΉ Example: OSHA fined a refinery for not providing confined space training, leading to stricter compliance in the industry.
π 1.2 Lockout/Tagout (LOTO) Procedures for Pipeline Maintenance π§π
β LOTO prevents unexpected energy release during maintenance.
β OSHA requires:
β
Isolation of electrical, hydraulic & gas-powered systems before repair.
β
Tagging and locking of pipeline valves & equipment.
β
Worker training on energy control protocols.
πΉ Example: A pipeline explosion was prevented by strict LOTO compliance, avoiding hazardous gas release.
π 1.3 Fire Safety & Explosion Prevention in Refineries π₯π
β Oil & gas facilities handle flammable liquids & explosive gases, requiring strict fire safety regulations.
β OSHA mandates:
β
Flame-resistant safety zones around high-risk areas.
β
Fire suppression systems (foam, COβ, water sprinklers).
β
Proper storage & handling of volatile chemicals.
πΉ Example: A well-trained response team & automated shutdown system prevented a refinery fire from escalating.
β 2. HSE (Health, Safety & Environment) Best Practices ππ
β HSE focuses on minimizing workplace risks, environmental impact, and ensuring worker safety.
β Key safety measures include:
π 2.1 Hazard Identification & Risk Assessment (HIRA) β Preventing Workplace Accidents β οΈ
β Before starting any work, hazards must be identified & mitigated.
β HIRA assessments evaluate:
β
Potential fire & explosion risks in refinery units.
β
Gas leak & pipeline rupture scenarios.
β
Equipment failure risks due to corrosion or overheating.
πΉ Example: A refinery improved worker safety by using HIRA to redesign storage tank layouts for better fire protection.
π 2.2 Process Safety Management (PSM) β Preventing Industrial Accidents π
β PSM is a structured approach to prevent major incidents in high-risk industries.
β OSHA & HSE regulations require:
β
Regular equipment inspections & predictive maintenance.
β
Proper training of workers handling hazardous materials.
β
Emergency shutdown systems for sudden leaks or pressure surges.
πΉ Example: A chemical plant explosion was prevented when a predictive AI system detected pipe overpressure before failure.
π 2.3 Emergency Response & Disaster Management β Fire Drills & Evacuation Plans π¨
β Proper planning reduces response time during industrial accidents.
β OSHA & HSE require:
β
Routine fire drills & worker evacuation training.
β
Spill containment systems for chemical leaks.
β
Emergency response teams with fireproof suits & gas masks.
πΉ Example: A refinery prevented an oil spill disaster by deploying rapid spill containment barriers within minutes of detection.
β 3. Case Study: How OSHA Regulations Prevented a Major Refinery Explosion β‘π
πΉ A U.S. refinery faced a potential catastrophic explosion due to corroded pipelines & gas leaks.
πΉ OSHA interventions led to:
3.1 Improved Worker Training & Safety Audits π
β
Mandatory safety audits identified weak points in pipeline maintenance.
β
Workers received enhanced hazardous material handling training.
3.2 Strengthened Pipeline Integrity Testing π
β
New AI-powered ultrasonic sensors detected pipeline weaknesses.
β
Corroded pipes were replaced before failure.
3.3 AI-Driven Predictive Maintenance β Preventing Future Accidents π€
β
Automated sensors monitored temperature, pressure & leak risks.
β
AI-based predictive maintenance reduced unplanned failures by 50%.
πΉ RESULT: The refinery avoided a multi-million dollar explosion & environmental disaster by following OSHA safety standards.
π Why OSHA & HSE Compliance is Critical in the Oil & Gas Industry
πΉ Prevents workplace accidents, saving lives & reducing injuries.
πΉ Reduces fire & explosion risks, protecting assets & the environment.
πΉ Ensures compliance with legal regulations, avoiding fines & shutdowns.
π OSHA & HSE standards make refineries and industrial plants safer, smarter, and more efficient! π
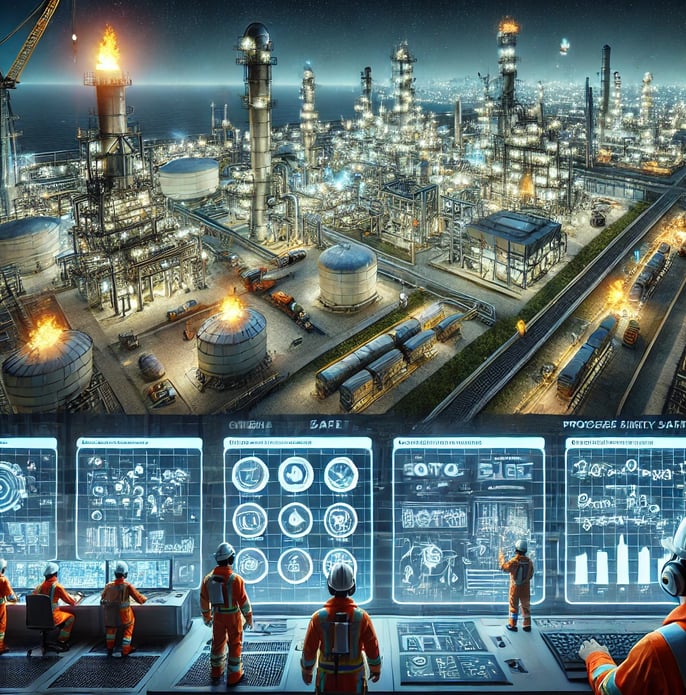
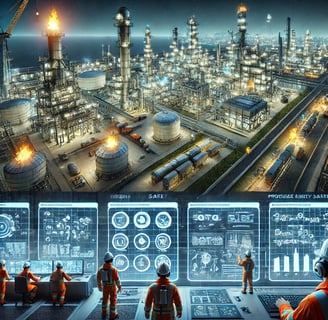
Environmental Compliance in Oil & Gas β Sustainability Regulations πβ‘
As concerns over climate change, carbon emissions, and environmental pollution grow, the oil & gas industry faces strict global regulations to reduce its impact. Governments and organizations enforce sustainability laws to ensure companies minimize emissions, prevent spills, and transition toward cleaner energy solutions.
β 1. Key Environmental Regulations βοΈπ±
1.1 EPA Clean Air Act β Reducing Air Pollution from Refineries & Pipelines π«π
β The EPA (Environmental Protection Agency) Clean Air Act regulates air pollutants from oil refineries, drilling sites, and gas pipelines.
β It targets:
β
Sulfur dioxide (SOβ) & nitrogen oxides (NOβ) β Linked to acid rain & respiratory diseases.
β
Methane (CHβ) emissions β A potent greenhouse gas from oil & gas production.
β
Volatile organic compounds (VOCs) β Contribute to smog and air pollution.
πΉ Example: Refineries must install air scrubbers to capture pollutants before they enter the atmosphere.
1.2 MARPOL Convention (IMO Regulations) β Preventing Marine Oil Spills ππ’
β The MARPOL Convention (Marine Pollution Treaty), enforced by the International Maritime Organization (IMO), regulates:
β
Marine oil spills from tankers & offshore rigs.
β
Disposal of toxic waste in oceans.
β
Sulfur cap on marine fuels (IMO 2020 rule limits sulfur content to 0.5%).
πΉ Example: Oil tankers must use double-hull designs to reduce spill risks.
1.3 Paris Agreement Carbon Reduction Goals β Encouraging Decarbonization β»οΈπ
β The Paris Agreement aims to limit global temperature rise below 1.5Β°C.
β Oil & gas companies must:
β
Cut COβ emissions from drilling & refining.
β
Invest in low-carbon fuels like hydrogen & biofuels.
β
Develop net-zero carbon strategies by 2050.
πΉ Example: BP & Shell are investing in carbon-neutral energy projects to comply with Paris goals.
1.4 Environmental Impact Assessments (EIA) β Approval for New Pipelines & Refineries π
β Before building new pipelines, refineries, or drilling sites, companies must:
β
Assess environmental risks & impact on local ecosystems.
β
Get government approval based on emission reduction plans.
β
Implement spill prevention & habitat protection measures.
πΉ Example: The Keystone XL Pipeline was canceled due to environmental concerns raised in its EIA.
β 2. How the Oil & Gas Industry is Adapting ππ
2.1 Carbon Capture & Storage (CCS) β Capturing COβ Before it Enters the Atmosphere π«
β CCS technology traps COβ emissions from refineries & power plants, storing them underground.
β Reduces global COβ emissions by up to 15% when widely adopted.
πΉ Example: Chevronβs CCS project in Australia captures 4 million tons of COβ per year.
2.2 Biofuels & Green Hydrogen β Reducing Dependence on Crude Oil π±π
β Biofuels from plant-based oils & algae can replace gasoline & diesel.
β Green hydrogen (Hβ) is produced using renewable energy, with zero carbon emissions.
πΉ Example: TotalEnergies is developing biofuel plants for aviation fuel, reducing emissions by 80%.
2.3 Zero-Discharge Technologies β Recycling Wastewater from Drilling Operations π°
β Oil drilling generates toxic wastewater, which must be treated & recycled.
β Zero-discharge systems purify & reuse drilling water, preventing environmental contamination.
πΉ Example: Saudi Aramcoβs offshore platforms recycle 95% of drilling water to reduce ocean pollution.
2.4 Low-Emission Refinery Operations β Using Solar, Wind & Hydroelectric Energy βοΈβ‘
β Oil refineries are reducing fossil fuel use by integrating renewable energy sources.
β Wind & solar power reduce operational emissions, improving energy efficiency.
πΉ Example: Shellβs Rheinland Refinery in Germany runs partially on solar power, cutting emissions by 30%.
π The Future of Sustainability in Oil & Gas
πΉ Carbon-neutral energy production will become the industry standard.
πΉ Hydrogen & biofuels will replace traditional fossil fuels.
πΉ AI & automation will improve energy efficiency & reduce emissions.
π The oil & gas industry is transforming toward a cleaner, greener future! π
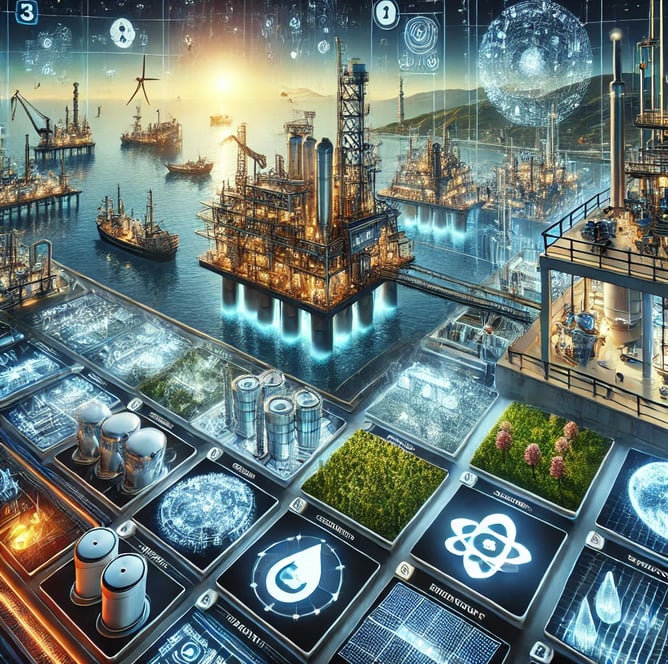
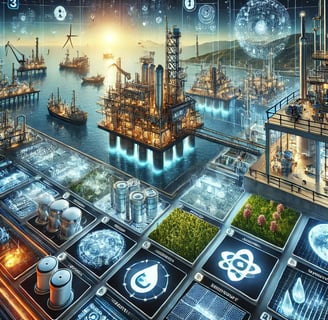