π Latest Technologies in Piping & Oil & Gas β The Future of
Energy & Infrastructure! π
The oil & gas and piping industries are undergoing a technological revolution with cutting-edge innovations improving efficiency, safety, and sustainability. This course explores emerging trends that are reshaping the industry, making processes smarter, more automated, and environmentally friendly.
Digital Twin Technology β Revolutionizing Piping & Oil & Gas Operations
Digital Twin technology is transforming the oil & gas industry by enabling real-time monitoring, predictive maintenance, and operational optimization. By creating a virtual replica of physical assets, companies can simulate performance, predict failures, and enhance decision-making.
1. What is a Digital Twin?
1.1 Definition
A Digital Twin is a real-time virtual model of a physical asset, process, or system that uses live data, AI, and IoT sensors to simulate performance and predict future conditions.
1.2 Key Features of Digital Twins
Real-time Monitoring: Sensors continuously update the virtual model with live data.
Predictive Insights: AI & machine learning analyze patterns and detect failures before they happen.
Optimization & Simulation: Engineers test different operational strategies before applying them to physical systems.
1.3 Benefits of Digital Twin Technology
β 2. How Digital Twin Works?
Digital Twins combine multiple technologies to create an interactive, real-time simulation of physical assets.
2.1 Core Technologies Used in Digital Twins
2.2 How the Digital Twin Process Works
Data Collection: Sensors gather information on pressure, temperature, vibration, and flow rates.
Digital Modeling: A 3D simulation of the equipment is created based on real-time and historical data.
AI-Powered Analytics: Machine learning detects anomalies and predicts failures.
Decision-Making & Optimization: Engineers use the digital twin to test scenarios before applying changes to the real system.
β 3. Applications in Piping & Oil & Gas
Digital Twin technology is widely used across pipelines, refineries, offshore platforms, and petrochemical plants.
3.1 Pipeline Integrity Monitoring β Detect Leaks, Corrosion, and Stress Points
Digital Twins monitor pipeline pressure, flow rates, and material integrity.
AI detects leaks, corrosion, and stress anomalies before they cause failures.
Example: TransCanada uses Digital Twins to predict pipeline corrosion and optimize maintenance schedules.
3.2 Refinery Process Optimization β Improve Efficiency & Reduce Downtime
Digital Twins simulate refinery processes, helping optimize:
Heat exchangers
Distillation towers
Catalytic cracking units
Reduces energy consumption and emissions while maximizing yield.
Example: ExxonMobil improved refining efficiency by 8% using Digital Twins.
3.3 Offshore Platform Management β Predict Maintenance Needs Before Failures Occur
Offshore rigs face harsh environmental conditions leading to rapid equipment degradation.
Digital Twins predict equipment failures, reducing offshore shutdowns.
Example: BP uses Digital Twins for remote offshore monitoring, reducing inspection costs by 20%.
β 4. Case Study: How BP & Shell Use Digital Twins to Optimize Offshore Rigs
4.1 BPβs Digital Twin Implementation
BP uses AI-powered digital twins for its offshore platforms.
The technology monitors drilling performance, detects equipment wear, and optimizes well output.
Results:
20% reduction in maintenance costs.
15% increase in operational efficiency.
4.2 Shellβs Digital Twin for Oil Rig Safety
Shell deployed a real-time digital twin for offshore rig safety.
The system predicts well pressure fluctuations and prevents blowouts.
Results:
Reduced risk of offshore accidents.
Lowered emissions by optimizing fuel use.
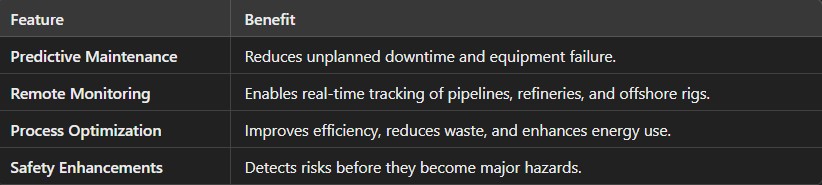
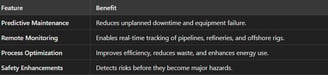
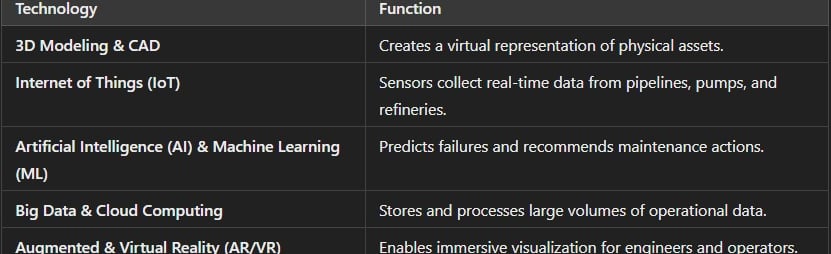
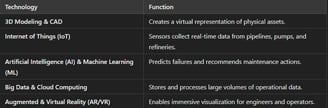
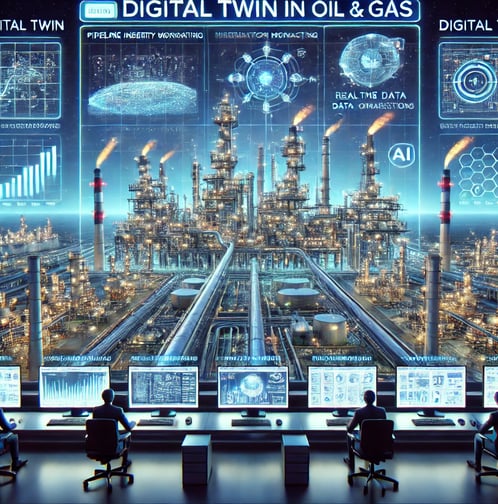
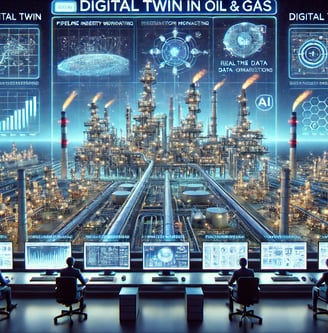
AI & Machine Learning in Piping β The Future of Automation & Predictive Maintenance
Artificial Intelligence (AI) and Machine Learning (ML) are transforming the piping, oil & gas, and industrial sectors by enabling automation, predictive maintenance, and data-driven decision-making. AI-powered systems reduce operational costs, improve efficiency, and enhance safety by identifying potential failures before they occur.
β 1. AI in Piping & Oil & Gas
AI is being applied across the piping and oil & gas industries to enhance efficiency, reduce downtime, and optimize operations.
1.1 Predictive Maintenance β AI Detects Early Signs of Equipment Failure
Traditional maintenance methods rely on periodic inspections, leading to unexpected breakdowns.
AI-powered Predictive Maintenance (PdM) uses:
IoT sensors to track real-time equipment conditions.
AI models to detect anomalies in pressure, temperature, and vibrations.
Benefits:
Reduces downtime by predicting failures before they happen.
Extends equipment lifespan by performing maintenance only when necessary.
Decreases maintenance costs by preventing unnecessary shutdowns.
1.2 Process Automation β AI-Powered Robots for Inspections, Welding & Drilling
AI-driven robotic systems perform inspections, welding, and drilling in dangerous environments.
Applications:
Automated pipeline inspection drones detect leaks and corrosion.
AI-controlled welding robots improve the precision of pipe welding in offshore rigs.
Drilling automation systems optimize drill bit placement to maximize efficiency.
Benefits:
Enhances worker safety by minimizing human exposure to hazardous conditions.
Speeds up construction & repairs with robotic automation.
Improves quality control through AI-powered defect detection.
1.3 Data-Driven Decision Making β AI Optimizes Operations Using Real-Time & Historical Data
AI analyzes historical trends and real-time sensor data to make accurate decisions.
Examples:
Pipeline control centers use AI to adjust flow rates and pressure dynamically.
AI-based refinery simulations optimize fuel output based on real-time market demand.
Benefits:
Reduces waste and inefficiencies in industrial processes.
Helps companies adapt to changing energy demands and optimize supply chains.
β 2. Machine Learning Algorithms in Use
Machine learning (ML) algorithms play a crucial role in automated fault detection, failure prediction, and optimization.
2.1 Anomaly Detection β Identifying Pipeline Leaks & Corrosion
AI-based pipeline monitoring systems use ML to detect leaks and corrosion by:
Analyzing pressure drops & flow inconsistencies in real time.
Using thermal imaging & ultrasonic sensors to detect corrosion before failure.
Example:
BP uses AI-powered monitoring to detect small leaks before they become hazardous spills.
Benefits:
Prevents environmental damage from pipeline ruptures.
Reduces repair costs by identifying problems early.
2.2 Predicting Equipment Lifespan β AI Forecasts When to Replace Critical Components
ML algorithms predict the remaining lifespan of pipes, valves, and pumps.
AI considers factors like:
Operating conditions (temperature, pressure, vibrations).
Material degradation over time.
Example:
ExxonMobil uses AI-driven predictive maintenance to extend the life of critical refinery equipment.
Benefits:
Reduces unplanned shutdowns.
Improves maintenance planning and budgeting.
2.3 Supply Chain Optimization β AI Enhances Logistics, Reducing Costs
AI optimizes supply chains by predicting:
Material shortages & delays.
Optimal transportation routes for pipes, fuel, and drilling equipment.
Example:
Shell uses AI logistics to improve fuel delivery times and reduce waste.
Benefits:
Cuts down operational costs by avoiding material shortages.
Improves just-in-time delivery for refinery components.
β 3. Real-World Example: How ExxonMobil Uses AI-Driven Predictive Maintenance
3.1 ExxonMobilβs AI Implementation
Problem:
Equipment failures in refineries caused unplanned shutdowns, leading to revenue losses.
Solution:
ExxonMobil deployed AI-driven predictive maintenance using IoT sensors and ML analytics.
Results:
Reduced maintenance costs by 25%.
Decreased equipment failures by 40%.
Improved energy efficiency across refineries.
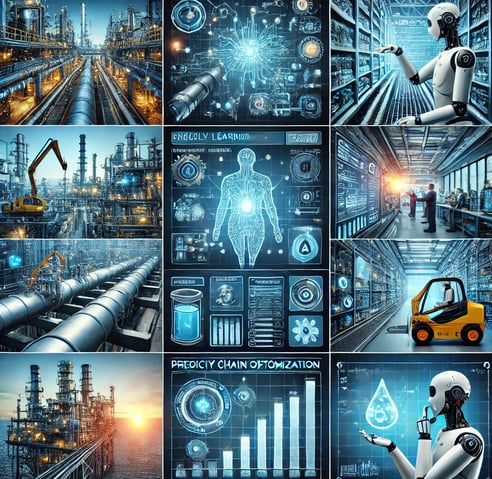
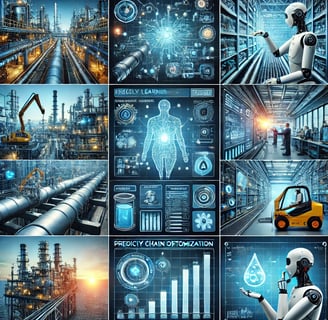
Smart Sensors & IoT in Pipelines β Enhancing Efficiency & Safety
The integration of smart sensors and IoT (Internet of Things) technology in pipelines and oil & gas operations is revolutionizing the industry. These technologies allow for real-time monitoring, automated control, and predictive maintenance, enhancing efficiency, safety, and cost savings.
β 1. What Are Smart Sensors?
1.1 Definition
Smart sensors are IoT-enabled devices that collect real-time data on pressure, temperature, vibration, flow rate, and leak detection.
These sensors are integrated with AI and cloud computing for remote analysis and decision-making.
1.2 Key Functions of Smart Sensors in Pipelines
1.3 How Smart Sensors Work
Collect Data β Sensors continuously monitor pipeline conditions.
Transmit Data β Data is sent via IoT networks (Wi-Fi, LTE, satellite, or LoRaWAN).
Analyze & Predict β AI & machine learning detect anomalies and predict failures.
Take Action β Automated systems can shut off valves or trigger maintenance alerts.
β 2. How IoT is Transforming Piping & Oil & Gas
IoT technology is enhancing pipeline management by enabling real-time tracking, predictive maintenance, and automated safety protocols.
2.1 Remote Monitoring β Track Pipeline Health from Anywhere
IoT sensors provide real-time data to control centers worldwide.
Operators can monitor pressure, temperature, and flow rates remotely.
Example:
Shell uses IoT for remote monitoring of offshore oil platforms.
Reduces on-site personnel, improving safety.
2.2 Leak Detection β Pinpointing Leaks Before Major Failures
AI-powered IoT sensors detect microscopic leaks before they become catastrophic.
Sensors measure:
Unusual pressure drops in pipelines.
Gas emissions indicating leaks.
Temperature differences caused by escaping fluids.
Example:
BPβs IoT leak detection system reduced pipeline failures by 35%.
2.3 Automated Control Systems β IoT-Enabled Valves Adjust Flow Rates Automatically
IoT smart valves automatically adjust flow rates and pressure.
Sensors detect blockages, re-routing fluids through alternate pathways.
Benefits:
Reduces pipeline downtime.
Prevents overpressure conditions and blowouts.
Example:
Chevron implemented IoT-controlled valves, reducing energy waste by 20%.
β 3. Innovative Applications of Smart Sensors & IoT
3.1 Drones & Robots for Inspections β Reducing Human Intervention in Hazardous Areas
Autonomous drones inspect long pipelines in remote areas.
Robots with cameras & ultrasonic sensors assess pipeline wall thickness & corrosion.
Example:
Saudi Aramcoβs pipeline inspection drones monitor over 6,000 km of pipelines.
3.2 AI-Connected Pipelines β Real-Time Data Sent to AI Dashboards for Analytics
IoT integrates with AI to create intelligent pipelines.
AI analyzes historical & real-time data to:
Predict equipment failures.
Optimize flow rates based on demand.
Trigger automatic shutdowns in emergency situations.
Example:
ExxonMobilβs AI pipeline system cut maintenance costs by 30%.
β 4. Case Study: How Saudi Aramco Uses IoT for Real-Time Pipeline Monitoring
4.1 The Challenge
Saudi Aramco manages thousands of kilometers of pipelines across deserts and offshore fields.
Traditional inspections were manual, slow, and expensive.
4.2 The IoT Solution
Saudi Aramco deployed smart sensors, drones, and AI-driven analytics to monitor pipelines.
Data from thousands of sensors is analyzed in real time, allowing instant response to anomalies.
4.3 Results & Benefits
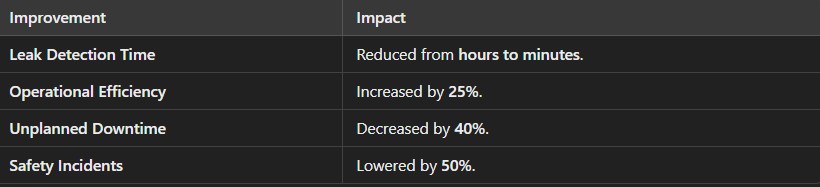
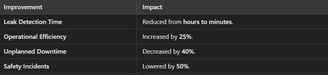
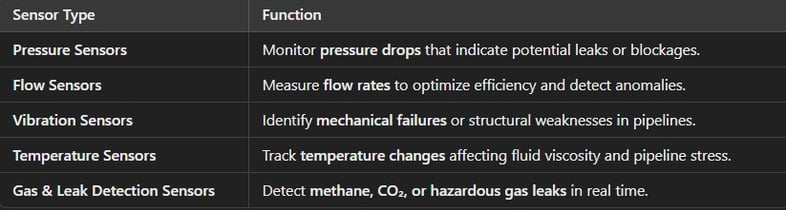
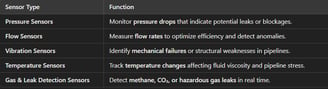
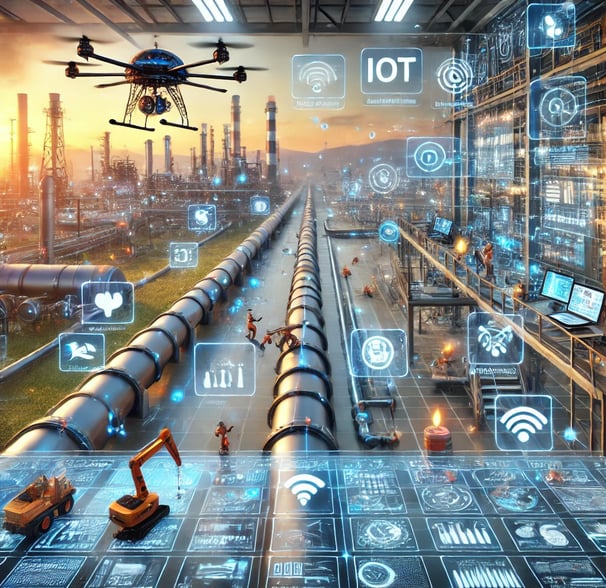
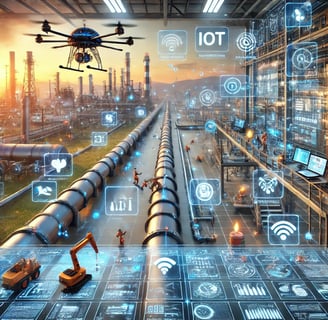
3D Printing for Piping Components β The Future of Manufacturing
3D printing, also known as Additive Manufacturing (AM), is revolutionizing the piping industry by allowing the creation of high-strength, customized, and lightweight piping components. This technology enables faster production, reduced material waste, and improved design flexibility compared to traditional manufacturing.
β 1. What is 3D Printing in Piping?
1.1 Definition
3D printing is an additive manufacturing process where layers of material are deposited, fused, and shaped to form a solid object. In the piping industry, it is used to manufacture:
Custom pipe fittings
High-strength valves & flanges
Complex piping geometries
Replacement components for refineries & power plants
1.2 How 3D Printing Works in Piping
3D Design (CAD Modeling) β Engineers create precise 3D models of piping components.
Material Selection β Metal powders (stainless steel, titanium, Inconel) or polymers are chosen.
Layer-by-Layer Printing β A laser or electron beam fuses materials into solid layers.
Post-Processing & Testing β Printed parts undergo heat treatment & quality checks for durability.
1.3 3D Printing Technologies Used in Piping
β 2. Advantages of 3D Printing Over Traditional Manufacturing
2.1 Rapid Prototyping β Quick Design & Testing of New Components
Engineers can quickly create prototypes of piping components for testing.
Traditional methods take weeks to months, while 3D printing reduces development time to days.
2.2 Reduced Material Waste β 50% Less Waste than Conventional Manufacturing
Traditional machining cuts materials, leading to waste.
3D printing builds parts layer by layer, using only the required material.
Reduces costs and minimizes environmental impact.
2.3 On-Demand Production β Eliminating Long Supply Chain Delays
Reduces dependence on global supply chains by manufacturing parts on-site.
Spare parts can be printed instantly, reducing downtime in oil refineries and power plants.
Example:
Shell 3D prints replacement pipeline valves at offshore rigs, reducing lead times by 60%.
β 3. Industries Using 3D Printing in Piping
3D printing is widely adopted across multiple industries for customized, high-performance piping components.
3.1 Oil Refineries β On-Site Production of Spare Parts
Refineries need durable, high-pressure piping for fuel processing.
3D printing allows rapid replacement of worn-out components.
Example:
Saudi Aramco uses 3D printing for high-temperature valve production.
3.2 LNG Plants β Custom Nozzles and Fittings for Extreme Temperatures
LNG plants operate at -162Β°C, requiring custom cryogenic piping.
3D printing allows precise fabrication of nozzles & heat exchangers resistant to extreme conditions.
Example:
ExxonMobil developed 3D-printed cryogenic pipe fittings to enhance LNG transport efficiency.
3.3 Aerospace & Defense β Complex Piping Systems for High-Pressure Environments
Used for high-performance fuel delivery systems in aircraft & military vehicles.
Allows the creation of lightweight, durable, and corrosion-resistant piping.
Example:
GE Aviation 3D prints fuel nozzles for jet engines, improving efficiency.
β 4. Case Study: How GE Oil & Gas Uses 3D Printing to Cut Costs & Improve Efficiency
4.1 The Challenge
GE Oil & Gas needed custom pipeline components for remote drilling operations.
Traditional manufacturing had long lead times and high costs.
4.2 The 3D Printing Solution
GE implemented metal 3D printing for rapid production of custom pipe fittings & valves.
Used DMLS (Direct Metal Laser Sintering) to create high-strength parts.
4.3 Results & Benefits
Impact: Saved millions in maintenance costs and reduced downtime for offshore oil rigs.


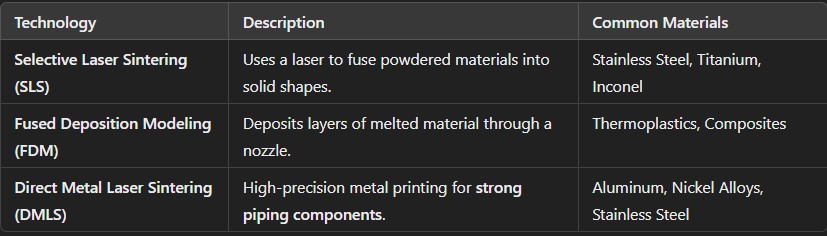
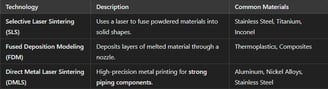
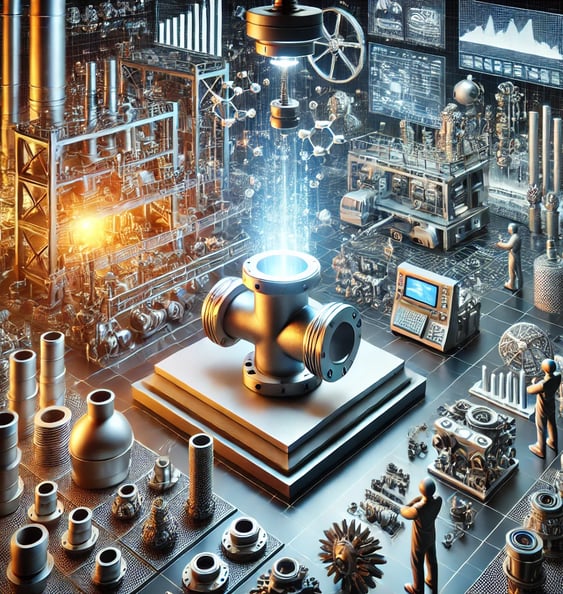
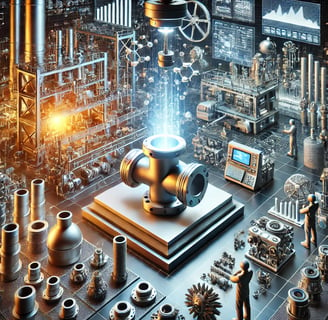
Green Technologies in Oil & Gas β Towards a Sustainable Future
The oil & gas industry is increasingly adopting green technologies to reduce environmental impact, improve energy efficiency, and comply with global sustainability regulations. These advancements are helping the industry transition toward a low-carbon future.
β 1. Why is Sustainability Important in Oil & Gas?
The oil & gas industry is one of the largest contributors to greenhouse gas emissions. Implementing green technologies helps reduce environmental impact while maintaining energy production.
1.1 Reducing Carbon Footprint β Lowering Greenhouse Gas Emissions
Oil & gas operations produce COβ, methane (CHβ), and nitrogen oxides (NOβ).
Reducing emissions helps mitigate climate change and improve air quality.
Key strategies include:
Carbon Capture & Storage (CCS) to prevent COβ emissions.
Methane leak detection & repair (LDAR) in pipelines.
1.2 Improving Energy Efficiency β Smart Technologies to Reduce Energy Waste
AI-powered monitoring systems optimize fuel consumption and reduce waste.
Waste heat recovery systems convert lost energy into usable power.
Upgrading equipment (e.g., low-emission turbines) enhances efficiency.
1.3 Complying with Regulations β Meeting Global Emission Targets
Many countries have set net-zero targets by 2050.
Regulatory frameworks include:
Paris Agreement (UN Climate Pact) β Reducing global carbon emissions.
EU Green Deal & US EPA Regulations β Promoting cleaner energy production.
International Maritime Organization (IMO 2020) β Limiting sulfur emissions in shipping fuel.
β 2. Innovative Green Technologies in Use
The oil & gas industry is investing in renewable energy, alternative fuels, and carbon-reducing technologies to create a more sustainable future.
2.1 Carbon Capture & Storage (CCS) β Capturing COβ Before It Enters the Atmosphere
What is CCS?
A process that captures COβ from industrial sources and stores it underground.
How it works:
COβ is captured at power plants or refineries.
Compressed and transported via pipelines.
Injected into deep geological formations for permanent storage.
Example:
Shellβs Quest CCS project in Canada captures 1 million tons of COβ annually.
2.2 Hydrogen Fuel Integration β Using Green Hydrogen as an Alternative Energy Source
What is Green Hydrogen?
Hydrogen produced using renewable energy (solar/wind-powered electrolysis).
Why is it important?
Can replace natural gas & diesel in refineries and power plants.
Produces zero COβ emissions when burned.
Example:
BP is investing $1 billion in green hydrogen production in the UK.
2.3 Solar & Wind-Powered Refineries β Reducing Dependence on Fossil Fuels
What is a Renewable-Powered Refinery?
Uses solar panels and wind turbines to power refinery operations.
Benefits:
Cuts emissions by 30-50%.
Lowers operating costs by reducing fuel consumption.
Example:
TotalEnergies uses solar power for oil production in the UAE.
2.4 Biofuels & Synthetic Fuels β Alternative Fuels to Cut Emissions
What are Biofuels?
Fuels made from organic materials (corn, algae, waste oils).
What are Synthetic Fuels?
Fuels created using COβ + Hydrogen (Power-to-Liquid Technology).
Benefits:
Can replace gasoline & diesel without modifying existing engines.
Lower COβ emissions compared to fossil fuels.
Example:
ExxonMobil produces biofuels from algae for aviation and transport.
β 3. Case Study: How BP is Investing in Green Hydrogen Projects
3.1 The Challenge
BP aims to cut carbon emissions by 50% by 2030.
Fossil fuel dependence is unsustainable in the long run.
3.2 The Green Hydrogen Solution
BP is developing green hydrogen plants powered by solar & wind energy.
Electrolysis technology splits water (HβO) into Hydrogen (Hβ) and Oxygen (Oβ) using renewable power.
3.3 Expected Benefits
BPβs green hydrogen hub in Australia & UK will play a major role in future clean energy production.


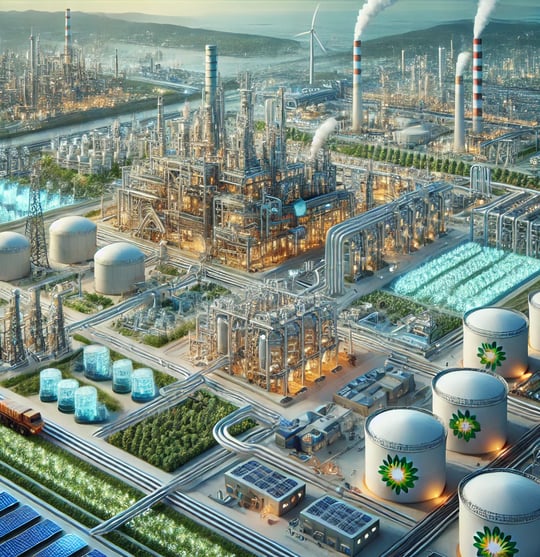
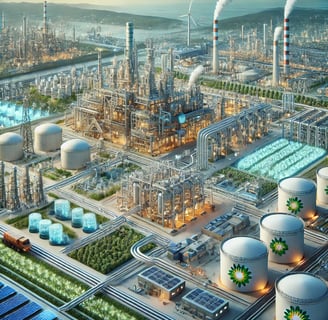