π Case Studies & Real-World Applications in Piping & Oil & Gas π
The oil & gas industry thrives on innovation, efficiency, and engineering excellence. This course explores real-world case studies, major successes, challenges, and emerging trends, providing valuable insights into pipeline design, cost optimization, and offshore engineering.
Successful Piping Projects β Breakdown of Major Oil & Gas Installations ππ’
Some of the worldβs most complex and advanced pipeline systems have set new benchmarks in engineering, resilience, and efficiency. These mega-projects transport crude oil and natural gas across continents, overcoming extreme environmental and geopolitical challenges.
β 1. Key Successful Piping Projects
1.1 Trans-Alaska Pipeline System (TAPS, USA) β Engineering Marvel in Harsh Terrain πβ
Location: Alaska, USA
Length: 1,300 km (800 miles)
Transport: Crude oil from Prudhoe Bay to Valdez Marine Terminal
Challenges Overcome:
Extreme Arctic temperatures (-60Β°C in winter).
Permafrost terrain requiring special insulation.
Earthquake-resistant pipeline design.
Innovation:
β Above-ground pipeline sections prevent permafrost melting.
β Thermal expansion joints allow flexibility during temperature changes.
β Remote monitoring ensures real-time leak detection.
1.2 Nord Stream Pipeline (Russia to Europe) β Deepwater Offshore Pipeline ππ₯
Location: Russia β Germany (under the Baltic Sea)
Length: 1,230 km (764 miles)
Transport: Natural gas to Europe via Germany
Challenges Overcome:
Deep-sea pipeline laying at depths of 110 meters (360 feet).
Cross-border geopolitical complexities.
Cold water corrosion risks mitigated by high-strength coatings.
Innovation:
β Steel-reinforced concrete coating to withstand deep-sea pressure.
β Automated pipeline inspection for leak detection.
β Environmental protection measures to avoid marine ecosystem damage.
1.3 TurkmenistanβChina Gas Pipeline β One of the Longest Gas Pipelines ππ’
Location: Turkmenistan β Uzbekistan β Kazakhstan β China
Length: 7,000 km (4,350 miles)
Transport: Delivers 55 billion cubic meters (bcm) of gas annually to China
Challenges Overcome:
Harsh desert climates and extreme heat in Central Asia.
Crossing multiple countries requiring international agreements.
Remote monitoring needed for border security & maintenance.
Innovation:
β Automated compressor stations optimize pressure balance.
β AI-driven monitoring systems detect leaks & gas flow inefficiencies.
β High-strength corrosion-resistant pipeline materials extend lifespan.
1.4 Shah Deniz Pipeline (Azerbaijan to Europe) β Enhancing Europeβs Energy Security π₯π
Location: Azerbaijan β Georgia β Turkey β Europe
Length: 3,500 km (2,175 miles)
Transport: Natural gas from the Caspian Sea to Europe
Challenges Overcome:
Deep-sea pipeline installation in the Caspian Sea.
Geopolitical tensions in the region.
Pipeline stability in earthquake-prone areas.
Innovation:
β Subsea pipeline design withstands high water pressure.
β Advanced gas processing stations for high-purity transport.
β Integration with Europeβs Southern Gas Corridor for energy diversification.
1.5 Saudi Aramcoβs Master Gas System β One of the Largest Gas Networks π₯π
Location: Saudi Arabia
Length: Over 4,000 km (2,485 miles)
Transport: Natural gas for domestic power plants & industries
Challenges Overcome:
Extreme desert temperatures exceeding 50Β°C (122Β°F).
Complex pipeline network linking gas fields across the kingdom.
Integration of hydrogen-ready infrastructure for future energy transition.
Innovation:
β AI-powered gas flow monitoring for real-time optimization.
β Smart leak detection reducing methane emissions.
β Hydrogen-ready pipelines for a future low-carbon economy.
β 2. Factors Behind Their Success
2.1 Innovative Materials β High-Strength & Corrosion-Resistant Coatings
Pipelines use advanced materials like:
β X80 steel grade for extreme pressure resistance.
β Polymer coatings to prevent corrosion in marine environments.
β Thermal insulation materials for Arctic and desert conditions.
2.2 Advanced Construction Techniques β Overcoming Extreme Challenges
Techniques used in mega-pipeline projects:
β Trenchless Technology β Avoids disturbing fragile ecosystems.
β Deepwater Installations β Underwater pipelines withstand ocean currents.
β AI-Driven Inspections β Drones and robots detect leaks before failures occur.
2.3 Optimized Design & Routing β Ensuring Maximum Efficiency
Engineers optimize routes by:
β Reducing pressure drops for energy-efficient transport.
β Minimizing flow restrictions to avoid blockages.
β Using seismic-resistant designs to withstand earthquakes.
π The Future of Pipeline Engineering
πΉ AI & IoT sensors will enhance real-time monitoring & predictive maintenance.
πΉ Smart pipelines with automatic leak detection will reduce environmental risks.
πΉ Hydrogen-ready infrastructure will drive the transition toward clean energy.
π As the world moves toward energy diversification, pipeline engineering will play a critical role in shaping global energy security. π
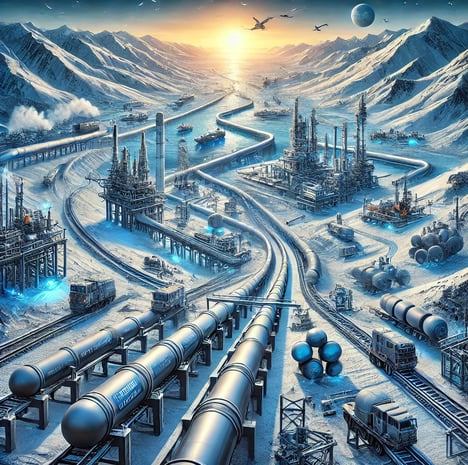
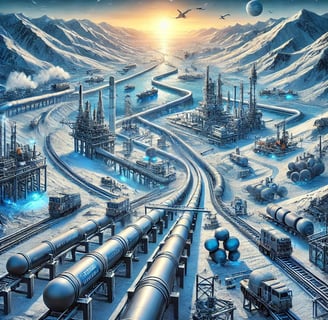
Challenges in Pipeline Design β Lessons from Industry Failures β π§
Pipelines are the lifelines of global energy infrastructure, transporting oil and gas safely across vast distances. However, failures in design, construction, and maintenance have led to catastrophic disasters, causing environmental damage, financial losses, and safety risks.
Learning from past failures is crucial for improving future pipeline designs and operational safety.
β 1. Major Pipeline Failures & Lessons Learned
1.1 Deepwater Horizon (2010, Gulf of Mexico) β The Worst Offshore Oil Spill ππ’
Incident: A blowout preventer (BOP) failure caused an uncontrolled well blowout, leading to an explosion and the largest offshore oil spill in history.
Oil Spilled: 4.9 million barrels into the Gulf of Mexico.
Cause:
β Weak well integrity & cement failure.
β Malfunctioning safety systems (BOP did not activate properly).
β High-pressure gas buildup in the wellbore.Lessons Learned:
β Stronger safety regulations for offshore drilling.
β Real-time well pressure monitoring to detect early warning signs.
β Improved blowout preventer (BOP) designs with automatic triggers.
1.2 San Bruno Pipeline Explosion (2010, USA) β Aging Pipeline Corrosion & Gas Leak π₯π₯
Incident: A natural gas pipeline explosion in California killed 8 people, destroyed 38 homes, and caused over $1 billion in damages.
Cause:
β Pipeline corrosion and undetected cracks.
β Lack of maintenance and outdated records.
β Failure of automated shutoff valves.Lessons Learned:
β Mandated smart sensors for real-time leak detection.
β AI-driven pipeline integrity monitoring.
β Increased inspections for aging pipeline networks.
1.3 Keystone XL Pipeline (USA-Canada) β Environmental & Policy Challenges ππ§
Incident: The pipeline was canceled in 2021 after years of delays due to environmental and political concerns.
Challenges Faced:
β Public opposition over environmental risks (water contamination, greenhouse gas emissions).
β Legal battles with Indigenous groups & landowners.
β Regulatory changes under different U.S. administrations.Lessons Learned:
β Future projects require extensive environmental impact studies.
β Community engagement & Indigenous partnerships are critical.
β Transitioning towards lower-carbon pipeline projects (hydrogen, biofuels, CCS).
1.4 Trans Mountain Pipeline (Canada) β Legal & Environmental Battles π²β
Incident: The pipeline expansion project faced years of legal challenges over environmental and Indigenous land rights concerns.
Challenges Faced:
β Opposition from environmental activists over oil spills risks.
β Indigenous communities raising land sovereignty issues.
β Court rulings delaying construction permits.Lessons Learned:
β Stronger community consultation & impact mitigation strategies.
β Enhanced spill response measures for environmentally sensitive areas.
β Incorporating Indigenous leadership in project planning.
1.5 Nigeria Oil Pipeline Leaks β Repeated Environmental Disasters ππ’
Incident: Continuous oil spills due to pipeline vandalism, aging infrastructure, and oil theft.
Environmental Damage:
β Severe pollution in the Niger Delta affecting communities.
β Marine and soil contamination destroying local ecosystems.Causes:
β Old and poorly maintained pipelines prone to leaks.
β Oil theft (bunkering) leading to pipeline sabotage.
β Limited government and corporate action on maintenance.Lessons Learned:
β Stronger pipeline protection measures & security.
β Increased use of advanced coatings & leak-proof materials.
β Strict enforcement of oil spill cleanup regulations.
β 2. Key Engineering Lessons for Future Pipeline Design
2.1 Material Selection is Critical β Using High-Grade Steel & Corrosion Protection π
β Pipelines must use advanced materials like:
β
X80/X100 high-strength steel for extreme pressure resistance.
β
Fusion-bonded epoxy coatings to prevent corrosion.
β
Thermal insulation for Arctic and deepwater pipelines.
2.2 Regular Maintenance & AI-Driven Monitoring β Preventing Failures Before They Happen ππ€
β Smart pipeline monitoring technologies include:
β
AI-powered leak detection sensors for real-time monitoring.
β
Drones for aerial pipeline inspections in remote areas.
β
Predictive maintenance using machine learning analytics.
2.3 Environmental & Regulatory Compliance β Meeting Global Safety Standards π±β
β Governments are enforcing stricter pipeline regulations, including:
β
Mandatory emergency shutoff valves (San Bruno explosion lesson).
β
Stronger environmental protection measures (Keystone XL lesson).
β
Indigenous land rights & community engagement (Trans Mountain lesson).
π The Future of Pipeline Safety & Engineering
πΉ AI-driven maintenance will predict failures before they occur.
πΉ Hydrogen-ready pipelines will replace traditional oil pipelines.
πΉ Stronger environmental compliance will make pipelines safer & cleaner.
π The pipeline industry is evolving toward a safer, smarter, and greener future! π
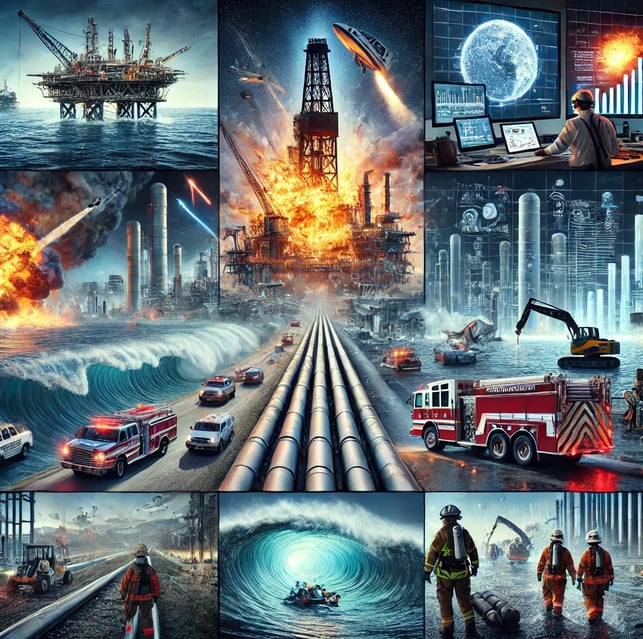
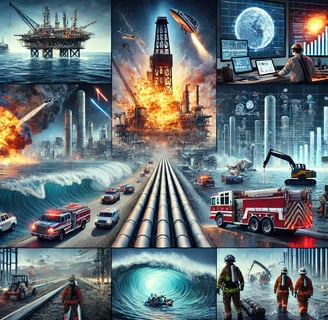
Cost Optimization in Piping Engineering β Improving Efficiency & Reducing Expenses π°βοΈ
Large-scale pipeline and refinery projects require huge capital investments, making cost control essential for profitability and sustainability. Companies that optimize expenses through technology, materials, and efficient processes can significantly reduce operational costs while improving pipeline longevity and performance.
β 1. Strategies for Cost Optimization
1.1 Efficient Material Selection β Reducing Long-Term Maintenance Costs π
β Choosing the right materials can reduce pipeline failures and extend service life.
β Traditional carbon steel pipes are prone to corrosion, leaks, and costly repairs.
πΉ Cost-Saving Alternatives:
β
Thermoplastic Composite Pipes (TCP): Lightweight, corrosion-resistant, and 40% cheaper in the long run.
β
Glass-Reinforced Epoxy (GRE) Pipes: Reduce corrosion-related costs by 30%.
β
Advanced Coatings: Polyethylene & epoxy coatings prevent pipeline rust & leaks, cutting maintenance costs.
1.2 Automation & AI-Driven Inspections β Reducing Manual Labor Costs π€π
β AI and automation can drastically reduce labor costs associated with pipeline maintenance.
β Traditional inspections involve manual pipeline patrols and costly shutdowns.
πΉ Cost-Saving Technologies:
β
Smart Sensors: Detect pressure drops, corrosion, and leaks in real-time.
β
Drones & Robotic Inspections: Monitor pipelines in hazardous or remote areas, reducing inspection costs by 60%.
β
AI-Powered Predictive Maintenance: Identifies potential failures before they happen, preventing expensive shutdowns.
πΉ Example: BP reduced inspection costs by 50% by deploying autonomous pipeline monitoring drones.
1.3 Modular Construction & Prefabrication β Faster & Cheaper Installation ππ
β Traditional on-site pipeline construction is expensive and time-consuming.
β Prefabricating pipe sections off-site reduces labor, material waste, and delays.
πΉ Cost-Saving Advantages:
β
Prefabricated piping modules cut installation time by 40%.
β
Factory-controlled quality ensures fewer defects & rework.
β
Lower transportation costs by using modular sections.
πΉ Example: ExxonMobilβs refinery expansion used modular pipe racks, reducing construction costs by 30%.
1.4 Energy Efficiency in Piping Systems β Reducing Fluid Loss & Heat Dissipation β‘π‘
β Energy losses in pipelines increase operating costs.
β Poor design leads to high pressure losses, turbulence, and inefficient fluid transport.
πΉ Cost-Saving Strategies:
β
Low-friction coatings inside pipes reduce turbulence & pumping costs.
β
Optimized pipeline routing reduces unnecessary bends & pressure drops.
β
Heat recovery systems minimize energy waste in heated pipelines.
πΉ Example: TotalEnergies improved refinery efficiency by 15% by upgrading piping insulation & flow control.
1.5 Supply Chain & Logistics Optimization β Cutting Transportation Costs ππ¦
β Pipeline projects involve massive amounts of materials, equipment, and logistics.
β Optimizing supply chains reduces transportation, procurement, and inventory costs.
πΉ Cost-Saving Strategies:
β
Bulk purchasing agreements lower pipe and valve costs.
β
AI-driven inventory management reduces material waste.
β
Just-in-time (JIT) deliveries prevent storage costs and delays.
πΉ Example: Chevron optimized its pipeline logistics, saving $20 million per year through AI-based supply chain analytics.
β 2. Case Study: How Shell Reduced Pipeline Costs by 25% π’π
Shell optimized its pipeline operations using advanced AI, new materials, and digital twin technology, resulting in a 25% cost reduction.
2.1 AI-Powered Predictive Maintenance
Deployed AI-based monitoring systems to detect pipeline issues before failure.
Reduced unplanned shutdowns, saving millions in repair costs.
2.2 Switched to Thermoplastic Composite Pipes (TCP)
Replaced traditional steel pipes with lightweight, corrosion-resistant TCP.
Lower maintenance costs & increased pipeline lifespan.
2.3 Adopted Digital Twin Technology for Real-Time Monitoring
Created a virtual replica of the pipeline network for real-time performance tracking.
Optimized flow efficiency & reduced operational energy consumption.
πΉ Result: Shellβs pipeline operating costs were reduced by $100 million over five years.
π The Future of Cost-Efficient Piping Engineering
πΉ AI & automation will further reduce inspection & maintenance costs.
πΉ Sustainable materials will replace traditional high-maintenance metals.
πΉ Digital twins & real-time monitoring will optimize efficiency & reduce energy waste.
π Pipeline projects are becoming smarter, greener, and more cost-effective! π
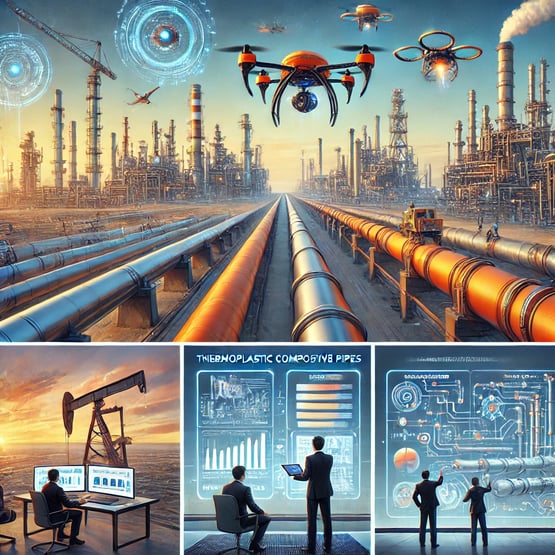
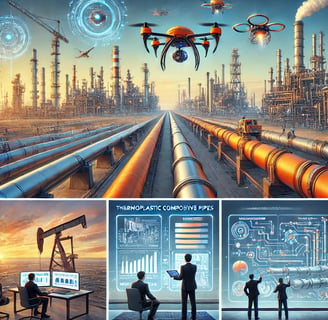
Innovations in Offshore Pipelines β How Deepwater Projects Are Managed ππ’
Offshore pipelines play a critical role in transporting oil and gas from deepwater reserves to refineries and markets. Operating in harsh underwater conditions, these pipelines require advanced engineering solutions to withstand extreme pressures, currents, and environmental challenges.
Write your text here...
β 1. Key Innovations in Deepwater Pipelines
1.1 Subsea Robots & ROVs β Next-Generation Pipeline Inspections & Maintenance π€π
β Remotely Operated Vehicles (ROVs) are revolutionizing deepwater pipeline inspection & repair.
β They replace human divers, making inspections safer, faster, and cost-effective.
πΉ Technology Benefits:
β
AI-powered robots detect corrosion & cracks before failures occur.
β
Autonomous underwater drones inspect pipelines in real time.
β
Robotic arms repair pipelines without stopping production.
πΉ Example: Equinor uses ROVs in the North Sea for continuous pipeline monitoring.
1.2 Floating Production Storage & Offloading (FPSO) β Offshore Processing Without Fixed Platforms π’π
β FPSOs allow oil & gas production in deepwater without requiring large fixed offshore rigs.
β These floating vessels extract, process, and store crude oil before transferring it to tankers.
πΉ Why FPSOs Are Game-Changers:
β
Reduces offshore drilling costs by 40%.
β
Can relocate to new drilling sites, unlike fixed platforms.
β
Improves oil recovery rates in ultra-deepwater fields.
πΉ Example: Shellβs Bonga FPSO in Nigeria can process 225,000 barrels of oil per day.
1.3 Flexible Pipe Technology β Adapting to Extreme Ocean Pressures & Currents π‘π
β Deepwater pipelines experience extreme water pressure & ocean movements.
β Flexible pipes are replacing rigid steel pipelines to improve durability & safety.
πΉ Advantages of Flexible Pipes:
β
Resist seabed movements & earthquakes.
β
Can operate in ultra-deepwater depths (>3,000 meters).
β
Reduce pipeline maintenance costs by 30%.
πΉ Example: Brazilβs Pre-Salt Oil Fields use flexible risers to transport crude oil.
1.4 Subsea Compression Systems β Boosting Gas Flow & Reducing Energy Losses πβ‘
β Gas pipelines lose pressure over long distances.
β Subsea compression stations maintain high flow rates, improving efficiency.
πΉ Why Itβs Important:
β
Extends the life of deep-sea gas fields by 10+ years.
β
Reduces energy consumption in gas transport.
β
Increases production from older gas wells.
πΉ Example: Equinorβs Γ sgard Subsea Compression System increased gas recovery by 50%.
1.5 Satellite Monitoring for Offshore Pipelines β Detecting Leaks & Movements Remotely π°π‘
β Satellites track pipeline shifts, temperature variations, and leaks from space.
β AI-powered satellite imaging detects oil spills faster than traditional sensors.
πΉ How It Works:
β
Real-time pipeline monitoring via thermal & radar satellites.
β
Early leak detection to prevent environmental disasters.
β
Geospatial AI predicts ocean current impacts on pipelines.
πΉ Example: BPβs Deepwater Horizon site now uses satellites for pipeline monitoring.
β 2. Successful Offshore Pipeline Projects
2.1 Nord Stream 2 (Baltic Sea) β Cutting-Edge Underwater Construction π’π§
Location: Russia β Germany
Length: 1,230 km (764 miles)
Depth: 110 meters (360 feet) underwater
Innovations:
β Concrete-coated steel pipes withstand deep-sea pressure.
β Automated trenching robots ensure seabed stability.
β Advanced leak detection sensors monitor gas flow.
2.2 West African Gas Pipeline (WAGP) β Energy Supply for Africa ππ₯
Location: Nigeria β Benin β Togo β Ghana
Length: 678 km (421 miles)
Capacity: 5 billion cubic meters per year
Innovations:
β High-resistance steel pipelines prevent gas loss.
β Floating platforms simplify pipeline maintenance.
β AI-powered flow monitoring optimizes gas distribution.
2.3 Perdido Pipeline (Gulf of Mexico, USA) β One of the Deepest Oil Pipelines in the World π’π
Location: Gulf of Mexico
Depth: 2,450 meters (8,000 feet) underwater
Capacity: 100,000 barrels of oil per day
Innovations:
β Deepwater risers prevent pipeline collapse.
β Subsea control units manage oil flow.
β Flexible pipe technology prevents rupture under pressure.
π The Future of Offshore Pipeline Technology
πΉ AI & robotics will handle most deep-sea pipeline inspections.
πΉ Hybrid materials will replace traditional steel pipelines.
πΉ Subsea storage & processing will reduce the need for surface platforms.
π Offshore pipelines are evolving to be safer, smarter, and more efficient! π
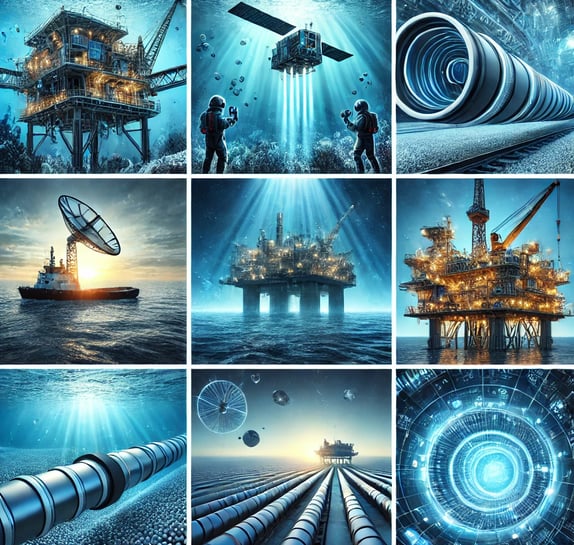
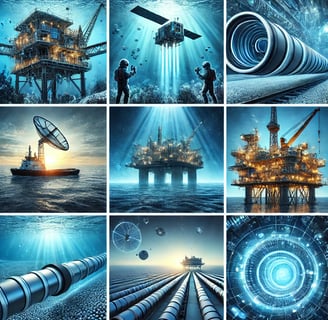
Future of the Oil & Gas Industry β Emerging Trends & Predictions πβ‘
With the world transitioning toward clean energy, the oil & gas industry is evolving to remain competitive. Companies are investing in renewables, carbon capture, AI-driven operations, and new fuel technologies to adapt to a low-carbon future.
β 1. Key Trends Shaping the Future
1.1 Carbon Capture & Storage (CCS) β Reducing Carbon Emissions in Refineries & Power Plants π«π
β CCS technology captures COβ emissions before they reach the atmosphere, preventing pollution.
β Why Itβs Important:
β
Reduces refinery carbon footprints by up to 90%.
β
Extends the lifespan of fossil fuel plants in a low-carbon world.
β
Companies like ExxonMobil & Chevron are investing billions in CCS.
πΉ Example:
ExxonMobilβs CCS Hub in Houston aims to store 100 million tons of COβ per year.
Saudi Aramco is developing carbon-neutral crude oil by integrating CCS in its refineries.
1.2 Hydrogen Energy & Biofuels β The Next Evolution in Oil & Gas ππ±
β Green hydrogen and biofuels are replacing traditional fossil fuels.
β Hydrogen energy is key for transportation, power generation, and industry.
β Biofuels (from plants, algae, & waste oils) offer a cleaner alternative to gasoline & diesel.
πΉ Why Hydrogen & Biofuels Matter:
β
Hydrogen can replace natural gas in refineries & transport.
β
Biofuels are already being used in aviation & heavy-duty vehicles.
β
BP & TotalEnergies are leading the charge in biofuel & hydrogen investments.
πΉ Example:
Shell is investing in a $2 billion green hydrogen project in Europe.
TotalEnergies is developing biofuel refineries for jet fuel.
1.3 AI-Driven Operations β The Rise of Automation in Oil & Gas π€π
β AI and automation are making the oil & gas industry more efficient and cost-effective.
β AI is used for:
β
Real-time pipeline monitoring to detect leaks & optimize flow.
β
Predictive maintenance to prevent failures before they happen.
β
Autonomous drilling & robotic inspections for deep-sea exploration.
πΉ Example:
Saudi Aramco uses AI-powered sensors to monitor its pipeline network.
ExxonMobilβs AI-driven drilling systems reduce energy waste by 30%.
1.4 Decline of Fossil Fuel Demand β The Impact of EVs & Renewables πβοΈ
β The global shift toward electric vehicles (EVs) and renewable energy is reducing oil demand.
β EV sales are expected to surpass gas-powered cars by 2035.
β Solar & wind power are replacing oil in electricity generation.
πΉ What This Means for Oil Companies:
β
Less demand for gasoline & diesel fuels.
β
Increased investments in alternative energy & carbon-neutral fuels.
β
Oil giants are shifting toward hydrogen & sustainable fuels.
πΉ Example:
BP expects oil demand to drop by 50% by 2050.
Chevron is investing in lithium extraction for EV batteries.
1.5 Decentralized Energy Grids β The Future of Distributed Power β‘π
β Traditional energy grids are centralized, relying heavily on fossil fuels.
β Decentralized energy grids use solar, wind & battery storage to create a more resilient system.
β Oil & gas companies are integrating renewables into their grids.
πΉ Why This Matters:
β
Less reliance on centralized fossil fuel plants.
β
More energy independence for homes & industries.
β
Integration of hydrogen fuel cells & battery storage.
πΉ Example:
Shell is building hybrid energy grids using solar & battery storage.
BP is investing in microgrids for industrial power supply.
β 2. How Oil & Gas Companies Are Adapting
π The oil industry is transforming from fossil fuels to sustainable energy solutions! π
π The Future of Oil & Gas β Whatβs Next?
πΉ Hydrogen will replace natural gas in industrial energy production.
πΉ AI-driven automation will optimize pipeline efficiency & reduce costs.
πΉ Carbon-neutral fuels will dominate transportation & shipping industries.
πΉ Oil majors will become clean energy giants in the next 20 years.
π± The industry is moving toward a cleaner, smarter, and more sustainable future! ππ
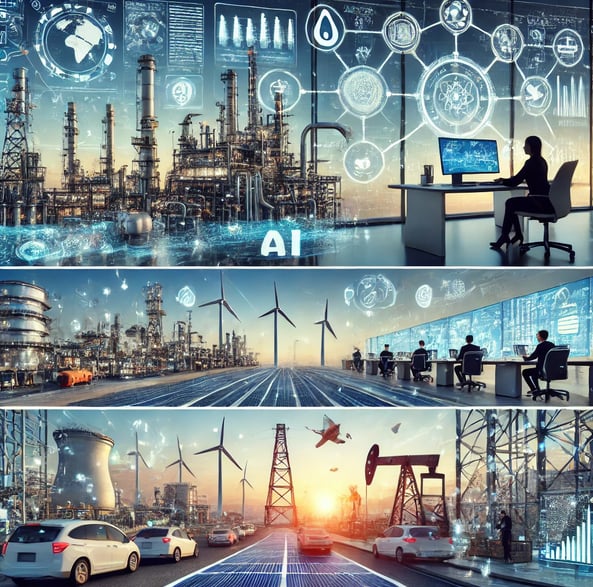
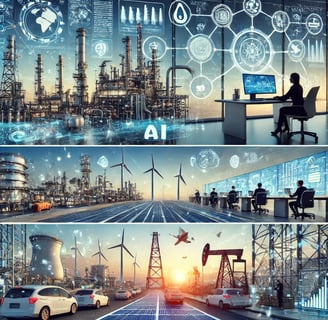

