🔥 Oil & Gas Industry Overview – Your Gateway to a Thriving Energy Sector!
The oil & gas industry is the backbone of global energy production, powering industries, transportation, and households. This is a deep dive into the industry’s operations, technology, and safety protocols to help you gain a competitive edge in this high-demand field.
✅ 1. Upstream (Exploration & Production)
The upstream sector involves the exploration, drilling, and extraction of crude oil and natural gas. It focuses on finding new oil fields, developing production techniques, and maximizing recovery rates.
1.1 How Oil & Gas Reservoirs Are Discovered
Seismic Surveys:
Geophysicists use seismic waves to map underground structures.
2D & 3D seismic imaging help locate potential oil & gas reservoirs.
Exploratory Drilling:
After seismic data analysis, test wells (wildcat wells) are drilled to confirm hydrocarbon presence.
1.2 Onshore & Offshore Drilling Operations
Onshore Drilling:
Done on land using rotary drilling rigs.
Common in Middle East, USA, Russia, and China.
Offshore Drilling:
Conducted in seas and oceans using:
Jack-up rigs (shallow water).
Semi-submersibles (deep water).
Floating production storage and offloading (FPSO) units (ultra-deep water).
1.3 Extraction Techniques & Enhanced Oil Recovery (EOR)
Primary Recovery: Uses natural pressure & pumps (limited to ~20% extraction).
Secondary Recovery: Involves water or gas injection to push oil toward wells (~30–50% extraction).
Enhanced Oil Recovery (EOR):
Uses steam injection, COâ‚‚ flooding, and chemical injection to maximize extraction beyond 50%.
✅ 2. Midstream (Transportation & Storage)
The midstream sector handles the transportation, storage, and distribution of crude oil, refined products, and natural gas.
2.1 Pipeline Networks, LNG Terminals, and Tanker Transport
Pipeline Networks:
High-pressure trunk pipelines carry crude oil & gas from fields to refineries.
Major pipeline systems include Trans-Alaska Pipeline & Keystone Pipeline.
LNG (Liquefied Natural Gas) Terminals:
Convert natural gas into liquid form (-162°C) for overseas transport.
Key LNG exporters: Qatar, USA, Australia.
Tanker Transport:
Crude oil tankers carry oil across oceans (e.g., VLCC & ULCC).
LNG carriers transport liquefied gas globally.
2.2 Crude Oil Storage and Distribution Systems
Strategic Petroleum Reserves (SPR):
Countries maintain large oil reserves for emergency supply disruptions.
Example: USA’s SPR holds over 700 million barrels.
Tank Farms & Storage Facilities:
Large above-ground tanks store crude oil before refining.
Refined products are stored in distribution terminals before market supply.
2.3 The Role of Midstream Companies in Global Energy Supply
Ensuring Global Oil Flow:
Pipelines and tankers move 100+ million barrels daily worldwide.
Key Players in Midstream:
Enbridge, TransCanada, Kinder Morgan (North America).
Saudi Aramco, Shell, BP, and Total (Global LNG & transport).
✅ 3. Downstream (Refining & Marketing)
The downstream sector processes crude oil into useful products like gasoline, diesel, jet fuel, and petrochemicals.
3.1 Processing Crude Oil into Fuels & Petrochemicals
Refineries convert crude oil into:
Fuels: Gasoline, diesel, jet fuel, marine fuel.
Petrochemicals: Plastics, fertilizers, synthetic rubber.
Lubricants & Waxes: Used in industrial & automotive applications.
3.2 Major Refining Processes
3.3 Gasoline, Diesel, Jet Fuel, and Other Refined Products
3.4 The Impact of Refineries on Global Markets
Oil Prices & Supply Chain:
Refineries adjust output based on global demand fluctuations.
OPEC & market speculation impact fuel prices.
Environmental Regulations:
Countries implement low-sulfur fuel mandates.
Carbon capture technologies are being integrated into refineries.
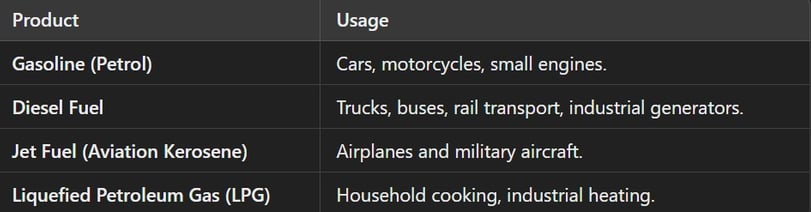
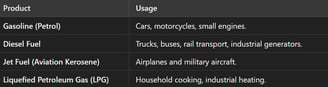
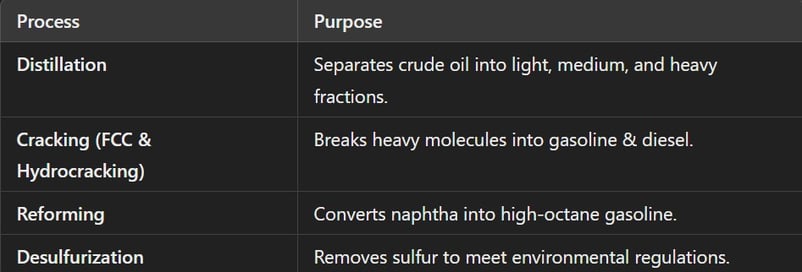
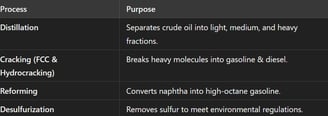
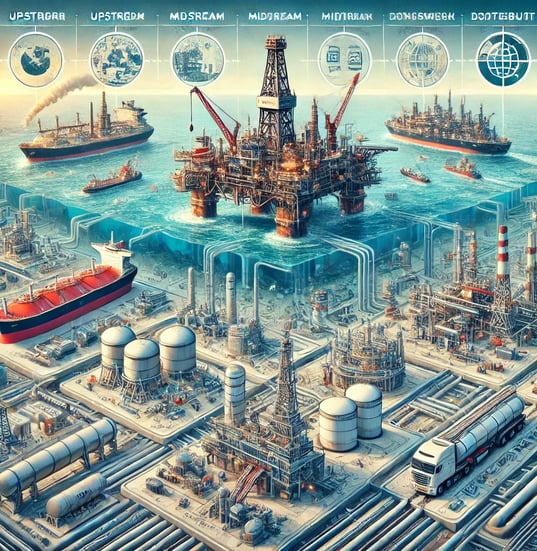
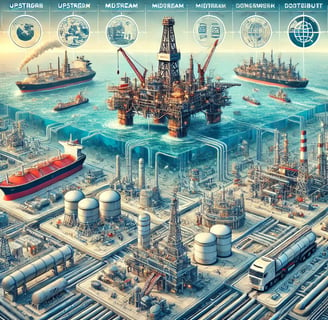
Upstream, Midstream & Downstream – Complete Industry Breakdown
The oil & gas industry is categorized into three major segments—Upstream, Midstream, and Downstream—each playing a critical role in the energy supply chain. Understanding these sectors helps grasp the complexities of how crude oil and natural gas are explored, transported, processed, and distributed globally.
Refinery Operations & Processes – How Crude Oil is Transformed
Refineries are highly complex facilities that process crude oil into useful fuels and petrochemical products. The transformation of crude oil involves physical and chemical processes to separate, upgrade, and purify various hydrocarbon components.
✅ 1. Crude Oil Composition & Properties
Before refining, it is essential to understand the composition and properties of crude oil. Different crude oils have varying characteristics that affect processing and product yields.
1.1 Key Properties of Crude Oil
✅ 2. Distillation Process – How Crude is Separated into Fractions
2.1 Primary Process: Fractional Distillation
Crude oil is heated to ~400°C and fed into a fractionating column.
Components separate based on boiling points:
Lighter hydrocarbons (gasoline, LPG) rise to the top.
Heavier hydrocarbons (diesel, fuel oil, bitumen) settle at the bottom.
2.2 Key Distillation Products
✅ 3. Major Refinery Units & Their Functions
Refineries consist of multiple processing units that convert raw crude fractions into high-value products.
3.1 Atmospheric & Vacuum Distillation – Primary Separation of Crude Oil
Atmospheric Distillation:
Separates crude oil under normal pressure into different fractions.
Products: Gasoline, diesel, kerosene, fuel oil.
Vacuum Distillation:
Used for heavier fractions that don’t vaporize under normal conditions.
Produces vacuum gas oil (VGO) and residuum, which are further processed.
3.2 Catalytic Cracking & Reforming – Breaking Heavy Hydrocarbons into Valuable Fuels
Catalytic Cracking (FCC – Fluid Catalytic Cracking):
Breaks long-chain hydrocarbons into gasoline and LPG using catalysts.
Used to increase gasoline production.
Catalytic Reforming:
Converts low-octane naphtha into high-octane gasoline.
Produces aromatics (benzene, toluene, xylene) for petrochemicals.
3.3 Hydrotreating & Hydrocracking – Removing Impurities Like Sulfur and Nitrogen
Hydrotreating:
Removes sulfur, nitrogen, and metals from fuels.
Produces low-sulfur diesel to meet environmental regulations.
Hydrocracking:
Uses hydrogen under high pressure to break heavy molecules.
Converts heavy gas oil into gasoline, jet fuel, and diesel.
✅ 4. Refinery Economics & Profitability – Understanding Refining Margins and Global Trends
4.1 Refining Margins – The Key to Profits
Refining margin = Selling price of refined products – Cost of crude oil.
Higher margins mean more profitable refinery operations.
4.2 Factors Affecting Refinery Economics
4.3 Future Trends in Refining
Biofuels & Renewable Diesel: Emerging as alternatives to fossil fuels.
Carbon Capture in Refineries: To meet climate goals.
Digital Optimization: AI and machine learning to improve efficiency.
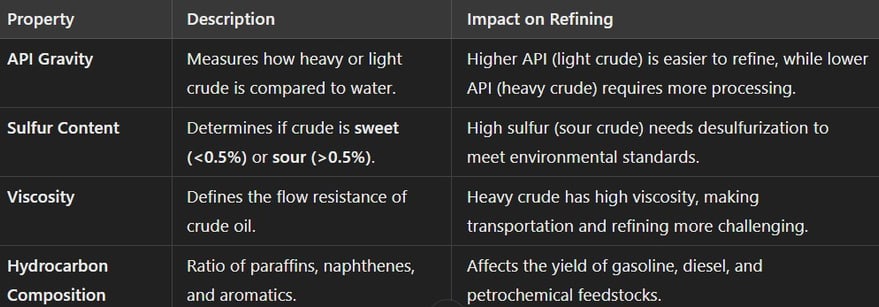
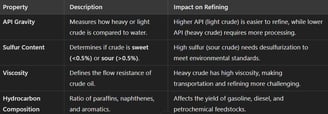
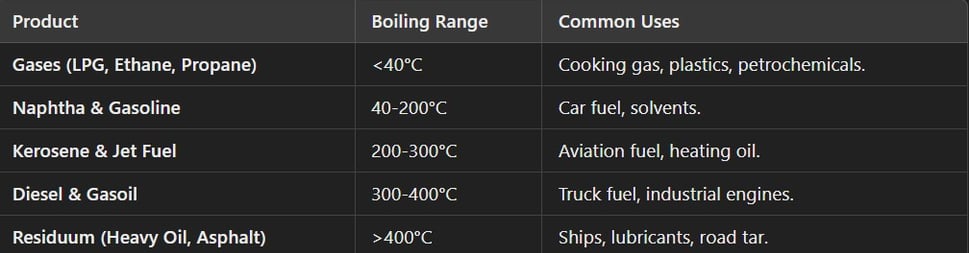

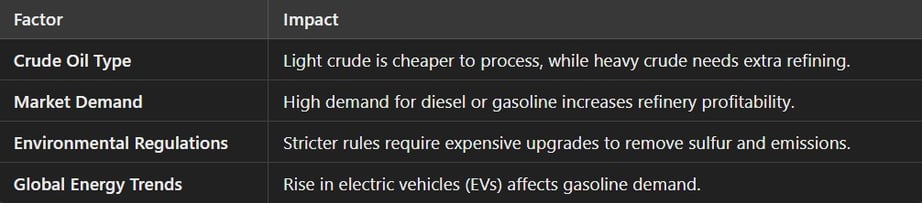
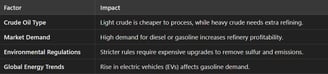
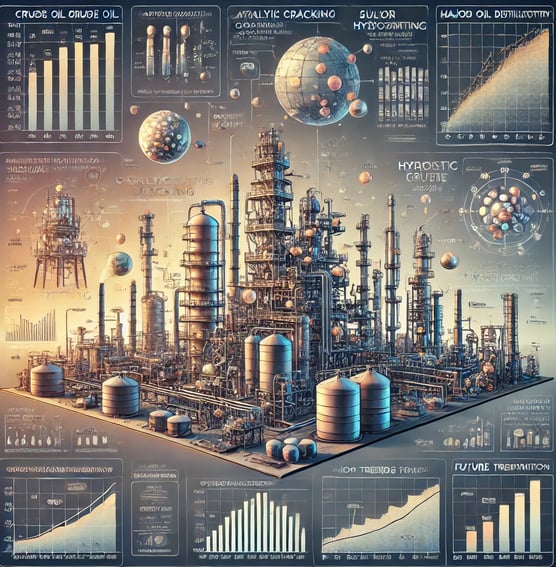
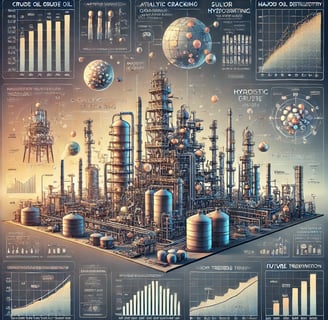
Liquefied Natural Gas (LNG) Technology – Storage & Transportation
Liquefied Natural Gas (LNG) is a clean-burning, energy-dense fuel that enables the efficient transportation of natural gas across long distances where pipelines are not feasible. By liquefying natural gas, its volume is reduced by approximately 600 times, making global trade and storage more efficient.
✅ 1. LNG vs. Pipeline Gas – Why Liquefy Natural Gas?
Natural gas is typically transported through pipelines or as LNG. The choice depends on cost, distance, and infrastructure availability.
1.1 Why is LNG Needed?
Pipelines are limited to land-based transport and are expensive to build across oceans.
LNG allows gas to be shipped globally to markets where pipelines are not available.
1.2 Comparison: LNG vs. Pipeline Transport
Conclusion: LNG is ideal for long-distance, international transport, whereas pipelines are better for continuous, regional supply.
✅ 2. Liquefaction Process – Converting Gas to Liquid at -162°C
2.1 What is Liquefaction?
Natural gas is cooled to -162°C to condense it into liquid form.
The process removes impurities (COâ‚‚, Hâ‚‚S, water) to prevent freezing during cooling.
2.2 LNG Production Steps
Pre-treatment: Removes COâ‚‚, water, and heavy hydrocarbons.
Cooling: Gas is progressively cooled in heat exchangers using refrigerants.
Liquefaction: At -162°C, gas turns into a liquid and is stored in cryogenic tanks.
2.3 Major LNG Liquefaction Technologies
✅ 3. LNG Shipping & Transportation – LNG Carriers & Export Terminals
Once liquefied, LNG is transported using specialized LNG carriers to global markets.
3.1 LNG Carriers (Tankers)
LNG tankers have cryogenic storage tanks to keep LNG cold.
Common tank designs:
Moss-type spherical tanks (more robust, but takes up more space).
Membrane tanks (higher capacity, commonly used).
3.2 Major LNG Exporting & Importing Countries
Largest LNG Exporters:
Qatar, USA, Australia, Russia
Largest LNG Importers:
China, Japan, South Korea, India, Europe
3.3 LNG Export Terminals
Receive pipeline gas, liquefy it, and load it onto LNG carriers.
Examples:
Sabine Pass LNG (USA)
Ras Laffan LNG (Qatar)
Ichthys LNG (Australia)
✅ 4. Regasification – How LNG is Converted Back to Usable Gas
Once LNG reaches its destination, it is converted back into gas (regasified) before being distributed to power plants and industries.
4.1 Regasification Process Steps
LNG is pumped to vaporizers.
Heated using seawater or air, converting it back to gas.
Gas is compressed and fed into pipelines for distribution.
4.2 Types of Regasification Terminals
4.3 Major Regasification Hubs
Japan, South Korea, India, China, Europe, and Brazil have large LNG import terminals.
✅ 5. Emerging Technologies – Floating LNG (FLNG) & Small-Scale LNG
5.1 Floating LNG (FLNG)
What is FLNG?
Offshore floating plants that liquefy natural gas at sea.
Advantages:
Avoids expensive onshore LNG plants.
Reduces land use & environmental impact.
Examples:
Prelude FLNG (Australia) – World’s largest FLNG facility.
PFLNG Satu (Malaysia) – First operational FLNG.
5.2 Small-Scale LNG (SSLNG)
Why SSLNG?
Suitable for remote regions & off-grid locations.
Enables LNG-powered transport (trucks, ships, trains).
Applications:
Industrial & mining operations.
LNG-powered ships & trucks (maritime fuel, trucking fleets).
5.3 Future Trends in LNG
Carbon-neutral LNG production.
Hydrogen & LNG blending.
Increased demand for LNG in shipping & power generation.
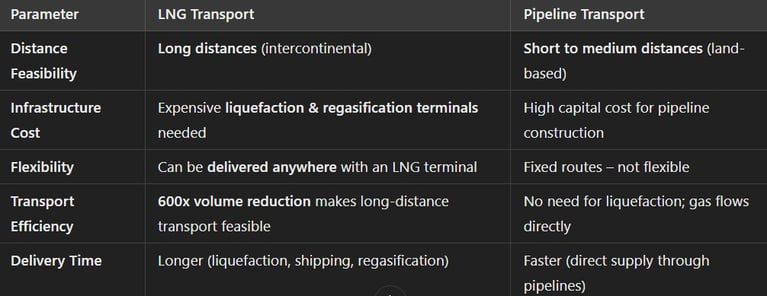
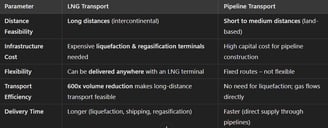


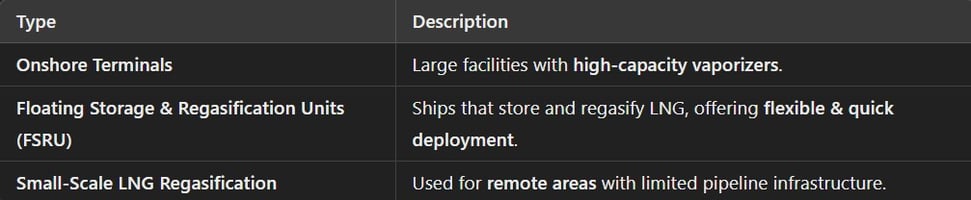

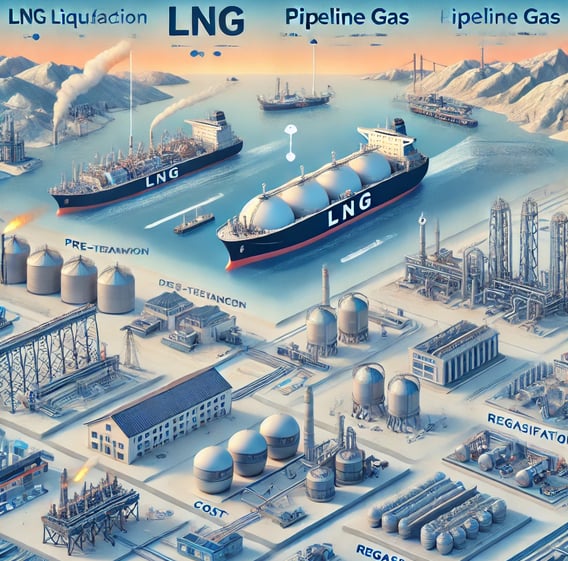

Safety Regulations & Best Practices – HSE Guidelines & Risk Management
The oil & gas industry involves high-risk operations, requiring strict Health, Safety & Environment (HSE) guidelines to prevent accidents, protect workers, and ensure environmental sustainability. Effective safety management reduces risks associated with fires, explosions, toxic gas leaks, and mechanical failures.
✅ 1. Major Safety Regulations in the Oil & Gas Industry
Various international and national safety regulations govern the industry to ensure workplace safety, environmental protection, and emergency preparedness.
1.1 OSHA (Occupational Safety & Health Administration) – Workplace Safety Standards
Regulates worker safety in hazardous industries, including oil & gas.
Key OSHA Standards for Oil & Gas:
OSHA 1910.119: Process Safety Management (PSM).
OSHA 1910.134: Respiratory Protection for toxic gases.
OSHA 1926: Construction safety for oil & gas sites.
1.2 API RP 14C – Offshore Safety Systems
Developed by the American Petroleum Institute (API).
Covers safety & risk assessment for offshore oil platforms.
Focuses on:
Pressure relief systems for blowout prevention.
Fire & gas detection systems for offshore safety.
Shutdown valves & emergency shutdown (ESD) protocols.
1.3 ISO 14001 – Environmental Management
Global standard for environmental safety in oil & gas operations.
Ensures:
Pollution control measures.
Waste management & spill response planning.
Compliance with climate change regulations.
✅ 2. Process Safety Management (PSM) – Preventing Accidents in High-Risk Facilities
2.1 What is PSM?
A systematic approach to identifying, assessing, and controlling hazards in industrial plants.
Required for industries handling highly hazardous chemicals.
2.2 Key Elements of PSM
2.3 Common PSM Failures Leading to Accidents
BP Texas City Refinery Explosion (2005) – Poor process safety, resulting in 15 deaths & 180 injuries.
Deepwater Horizon Disaster (2010) – Blowout preventer failure led to oil spill & explosion.
Piper Alpha Disaster (1988) – Inadequate emergency shutdown caused 167 fatalities.
✅ 3. Emergency Response & Disaster Management – Handling Fires, Spills & Explosions
3.1 Fire Prevention & Suppression Systems
Common Causes of Fires:
Flammable gas leaks (methane, propane).
Electrical sparks in hazardous areas.
Static discharge near fuel storage.
Fire Safety Equipment:
Fire-resistant coatings on pipelines.
Automatic fire suppression systems (deluge, foam, COâ‚‚ systems).
Explosion-proof electrical equipment in hazardous zones.
3.2 Oil Spill Management
Oil Spill Causes:
Pipeline ruptures.
Tanker accidents.
Well blowouts.
Response Strategies:
Booms & skimmers to contain spills.
Dispersants & bioremediation for cleanup.
Emergency containment dikes around storage tanks.
3.3 Explosion & Blowout Prevention
Blowout Preventers (BOPs) are critical safety devices in drilling rigs.
Venting & pressure relief systems prevent overpressure in tanks & pipelines.
✅ 4. Personal Protective Equipment (PPE) & Safety Protocols
4.1 Essential PPE for Oil & Gas Workers
4.2 Permit-to-Work (PTW) System
Ensures safety before high-risk tasks like:
Hot work (welding, grinding).
Confined space entry.
Working at heights.
4.3 Safety Culture & Worker Training
Behavior-Based Safety (BBS): Focuses on proactive safety behavior in workers.
HSE Training & Drills: Regular fire, spill, and emergency evacuation drills ensure preparedness.
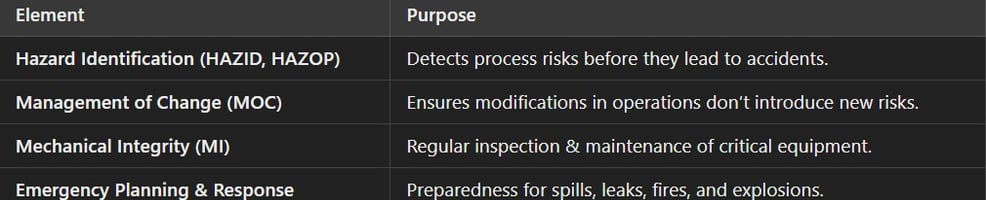
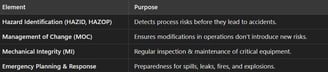
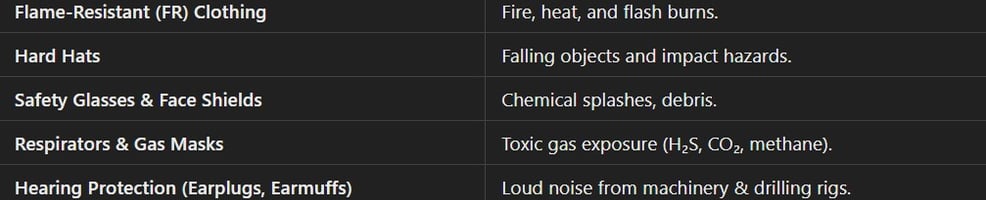
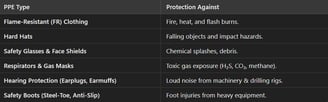
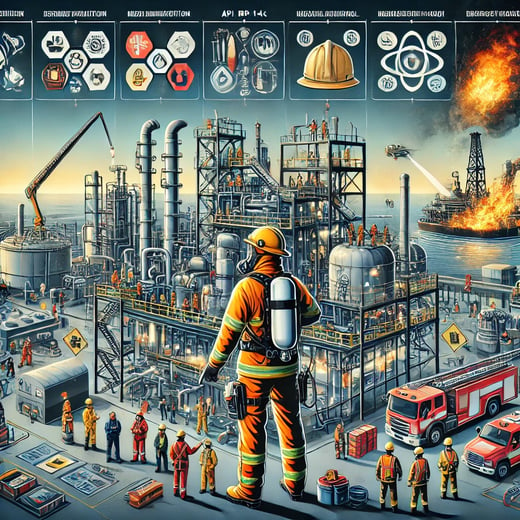
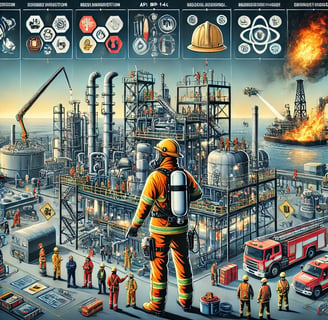
Oil & Gas Exploration Techniques – Onshore & Offshore Drilling
Oil & gas exploration is a highly technical process that involves advanced geophysical surveys, drilling techniques, and well completion to extract hydrocarbons efficiently. Exploration can take place onshore (land-based) or offshore (sea-based) using specialized drilling rigs and extraction methods.
✅ 1. Seismic Surveys – How Geologists Locate Oil & Gas Reserves
1.1 What Are Seismic Surveys?
Seismic surveys use sound waves to map subsurface rock formations.
Geologists analyze the reflected seismic waves to identify potential oil & gas reservoirs.
1.2 Types of Seismic Surveys
1.3 How Seismic Surveys Work
Sound waves are generated using air guns (offshore) or vibrators (onshore).
Waves travel through rock layers and reflect back to sensors (geophones).
Computers process the data to create geological maps of oil-rich zones.
1.4 Limitations of Seismic Surveys
Cannot confirm if oil is commercially viable.
Expensive and time-consuming process.
Some regions restrict seismic testing due to environmental concerns.
✅ 2. Drilling Rigs – Onshore vs. Offshore Platforms & Their Components
Once a potential oil reservoir is identified, drilling rigs are deployed to extract hydrocarbons.
2.1 Onshore Drilling Rigs
Land-based rigs are easier to set up and maintain.
Used in deserts, forests, and remote locations.
Key Components:
Derrick – Tall structure that supports drilling pipes.
Mud Pumps – Circulates drilling fluid (mud) to cool the drill bit.
Blowout Preventer (BOP) – Prevents uncontrolled well blowouts.
2.2 Offshore Drilling Platforms
2.3 Challenges in Offshore Drilling
Harsh ocean conditions (storms, high waves).
Logistics & supply chain issues (transporting equipment to rigs).
High operational costs compared to land drilling.
✅ 3. Directional & Horizontal Drilling – Maximizing Resource Extraction
3.1 What Is Directional Drilling?
Instead of drilling vertically, wells are drilled at an angle to reach oil reserves.
Benefits:
Access hard-to-reach reservoirs.
Minimizes land surface disturbance.
Increases well efficiency.
3.2 Horizontal Drilling – A Key Innovation
Extends the well horizontally within an oil-rich formation.
Used in combination with hydraulic fracturing (fracking).
Advantage: Extracts more oil from a single well, reducing drilling costs.
3.3 Real-World Example – Bakken Shale (USA)
Horizontal drilling helped boost U.S. shale oil production.
Enabled extraction from tight rock formations that were previously uneconomical.
✅ 4. Hydraulic Fracturing (Fracking) – Unlocking Shale Gas & Tight Oil
4.1 What Is Fracking?
Hydraulic Fracturing (fracking) is used to extract oil & gas from tight rock formations (shale).
High-pressure water, sand, and chemicals are injected to create fractures in the rock, allowing oil & gas to flow out.
4.2 Fracking Process Steps
Drilling: A well is drilled into a shale rock formation.
Fracturing Fluid Injection: Water, sand, and chemicals are pumped at high pressure.
Cracking the Rock: Fluid creates small fractures, allowing hydrocarbons to escape.
Production: Oil & gas flow to the surface through the wellbore.
4.3 Advantages of Fracking
Unlocks previously inaccessible oil & gas reserves.
Increases domestic energy production in countries like the USA.
Reduces dependence on imported oil.
4.4 Environmental Concerns
✅ 5. Well Completion & Production – Turning a Well into a Producing Asset
Once drilling is complete, the well must be prepared for continuous production.
5.1 Well Completion Process
Casing & Cementing
A steel casing is inserted into the wellbore.
Cement seals the casing to prevent leaks.
Perforation
Holes are created in the casing to allow oil & gas to flow.
Explosive charges (perforating guns) create small openings.
Production Tubing Installation
A smaller pipe is inserted to transport oil & gas to the surface.
Protects the wellbore from sand & debris.
Well Stimulation (Optional)
Fracking or acidizing may be used to increase production rates.
Production & Monitoring
Oil & gas flow to the surface and are sent to storage tanks & pipelines.
Sensors & control systems monitor pressure, flow rate, and temperature.
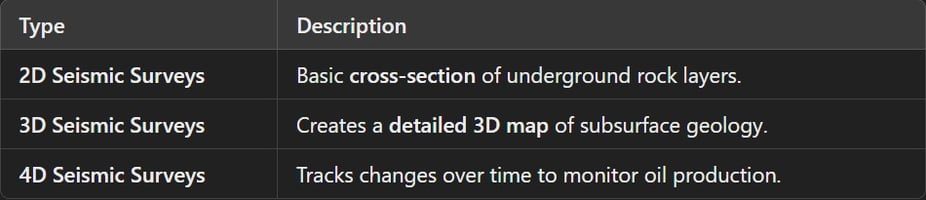
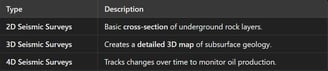
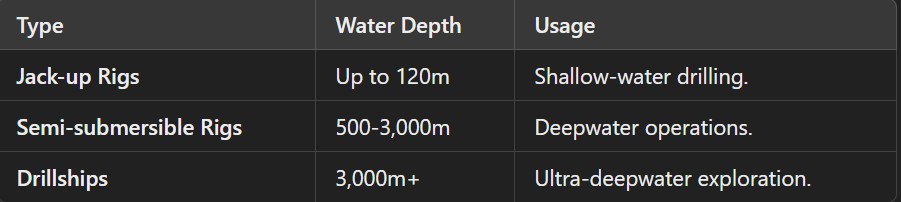
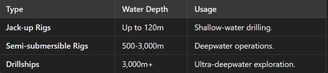
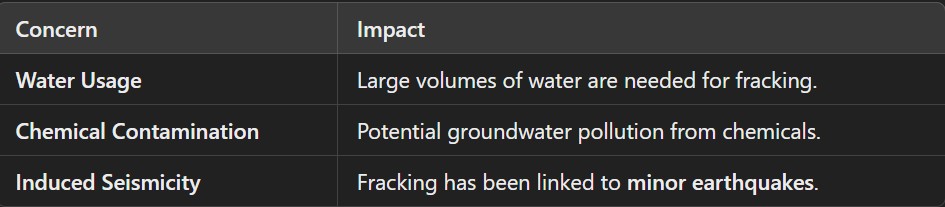
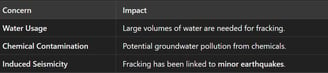
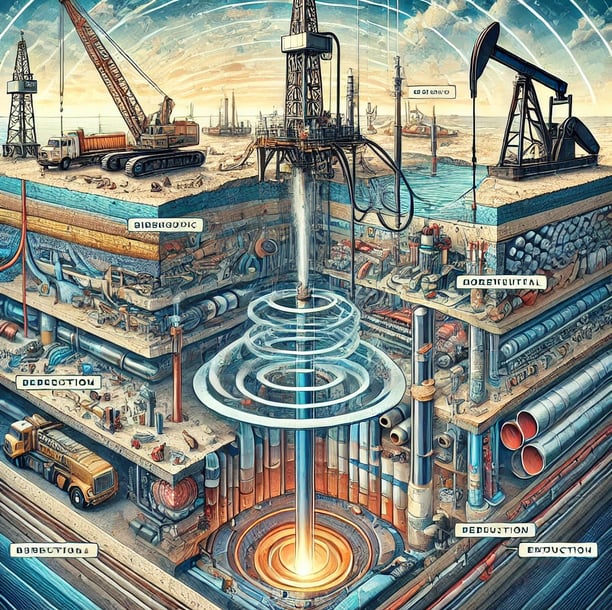
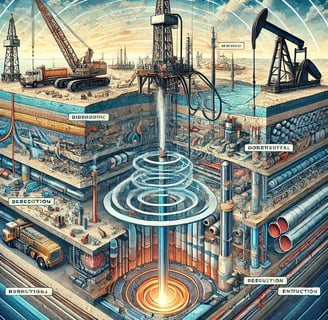