🚀 Piping System Components & Equipment – Essential Elements of Efficient Pipeline Design! 🔩
A well-designed piping system is crucial for safe and efficient transportation of fluids and gases in industries like oil & gas, power plants, and chemical processing. Explores critical piping components, their applications, functions, and industry best practices to ensure optimal performance and longevity.
Valves, Pumps & Fittings – The Core Components of Fluid Control 💧🔩
Valves, pumps, and fittings are essential components in piping networks, controlling flow, pressure, and direction of fluids. These components ensure efficient operation, safety, and reliability in industries such as oil & gas, refineries, water treatment, and power plants.
✅ 1. Types of Valves & Their Applications 🔄🔧
Valves regulate fluid flow by opening, closing, or partially obstructing passageways. The type of valve used depends on pressure, temperature, and fluid properties.
1.1 Gate Valve – Ideal for On/Off Control in Oil Pipelines 🚦🛢
✔ Gate valves are designed for full-flow shutoff applications.
✔ When open, they allow unrestricted flow with minimal pressure drop.
✔ Best suited for:
✅ Oil & gas pipelines
✅ High-pressure steam systems
✅ Underground water distribution
🔹 Example: Used in oil refineries to control crude oil transport with minimal pressure loss.
1.2 Globe Valve – Provides Precise Flow Regulation in Refineries 🔁🏭
✔ Globe valves control flow rate with adjustable throttling.
✔ Common in cooling water, fuel oil systems, and chemical processing.
✔ Best suited for:
✅ Refineries & chemical plants
✅ Boiler feedwater systems
✅ LNG & cryogenic applications
🔹 Example: Refineries use globe valves to fine-tune fluid flow in reaction vessels.
1.3 Ball Valve – Used for Quick Shutoff in High-Pressure Systems ⚡🔄
✔ Ball valves have a rotating ball mechanism for fast shutoff.
✔ Ideal for high-pressure, high-temperature applications.
✔ Best suited for:
✅ High-pressure gas pipelines
✅ Fire protection systems
✅ Hydraulic control systems
🔹 Example: Ball valves in offshore drilling rigs ensure rapid shutoff during emergency situations.
1.4 Check Valve – Prevents Backflow in Pumping Stations 🔄💦
✔ Check valves allow fluid to flow in one direction only.
✔ Prevents pump damage and contamination in pipelines.
✔ Best suited for:
✅ Water supply networks
✅ Oil pumping stations
✅ Steam power plants
🔹 Example: Water treatment plants use check valves to stop wastewater from flowing back into clean water lines.
1.5 Pressure Relief Valve (PRV) – Protects Against Overpressure & Explosions ⚠️🌡
✔ PRVs release excess pressure to prevent pipeline bursts.
✔ Required in boilers, refineries, and chemical processing.
✔ Best suited for:
✅ Steam boilers & pressure vessels
✅ Gas storage tanks
✅ Pipeline overpressure safety systems
🔹 Example: PRVs in refineries automatically release steam when pressure exceeds safe limits.
✅ 2. Types of Pumps & Their Industrial Use ⚙️💦
Pumps move fluids through pipelines using mechanical force. The type of pump depends on fluid viscosity, pressure requirements, and operating conditions.
2.1 Centrifugal Pumps – Used in Crude Oil Transport & Cooling Systems 🚀🛢
✔ Centrifugal pumps use rotating impellers to generate fluid flow.
✔ Ideal for large-volume, low-viscosity liquids.
✔ Best suited for:
✅ Crude oil pipelines
✅ Cooling water circulation in power plants
✅ Seawater desalination plants
🔹 Example: Refineries use centrifugal pumps to transfer crude oil between processing units.
2.2 Positive Displacement Pumps – Ideal for High-Viscosity Fluids Like Heavy Oil 🛢⚙
✔ Designed for thick, viscous fluids that cannot be pumped using centrifugal pumps.
✔ Delivers consistent flow even under pressure variations.
✔ Best suited for:
✅ Heavy oil, sludge, and asphalt transport
✅ Hydraulic systems & chemical dosing
✅ Oil tankers & offshore platforms
🔹 Example: Positive displacement pumps in heavy oil refineries improve flow in low-temperature conditions.
2.3 Submersible Pumps – Used in Deepwater Oil & Gas Extraction 🌊🔄
✔ Submersible pumps operate underwater, eliminating cavitation issues.
✔ Used for deep-sea drilling and groundwater extraction.
✔ Best suited for:
✅ Deepwater oil rigs & offshore platforms
✅ Groundwater pumping stations
✅ Floodwater control systems
🔹 Example: Submersible pumps in offshore oil fields lift crude oil from deep-sea reservoirs to surface facilities.
✅ 3. Fittings & Connectors 🏗🔩
Fittings connect pipes, change direction, and control flow within the piping network.
3.1 Elbows, Tees, and Reducers – Adjust Pipeline Flow Direction & Size ⛓
✔ Elbows change pipe direction (e.g., 45° or 90° turns).
✔ Tees allow branching into multiple directions.
✔ Reducers connect pipes of different diameters.
🔹 Example: Elbows & reducers in natural gas pipelines ensure smooth pressure transitions.
3.2 Threaded & Welded Fittings – Secure Pipe Connections in High-Pressure Environments 🏗🔧
✔ Threaded fittings are used for low-pressure applications.
✔ Welded fittings provide high-strength, leak-proof connections.
🔹 Example: Welded fittings in steam pipelines prevent leaks under high pressure.
3.3 Flanged Joints – Allow for Easy Maintenance & System Expansion ⚙️🔗
✔ Flanges enable quick assembly/disassembly of pipelines.
✔ Used in high-pressure and high-temperature systems.
🔹 Example: Flanged joints in refineries make it easier to replace pipes during maintenance.
🔍 Why Valves, Pumps & Fittings Matter in Piping Systems
🔹 Ensures precise fluid control & system reliability.
🔹 Protects pipelines from overpressure, backflow, and leaks.
🔹 Improves efficiency and reduces energy losses.
🚀 High-quality valves, pumps, and fittings are the backbone of industrial piping systems! 🌍
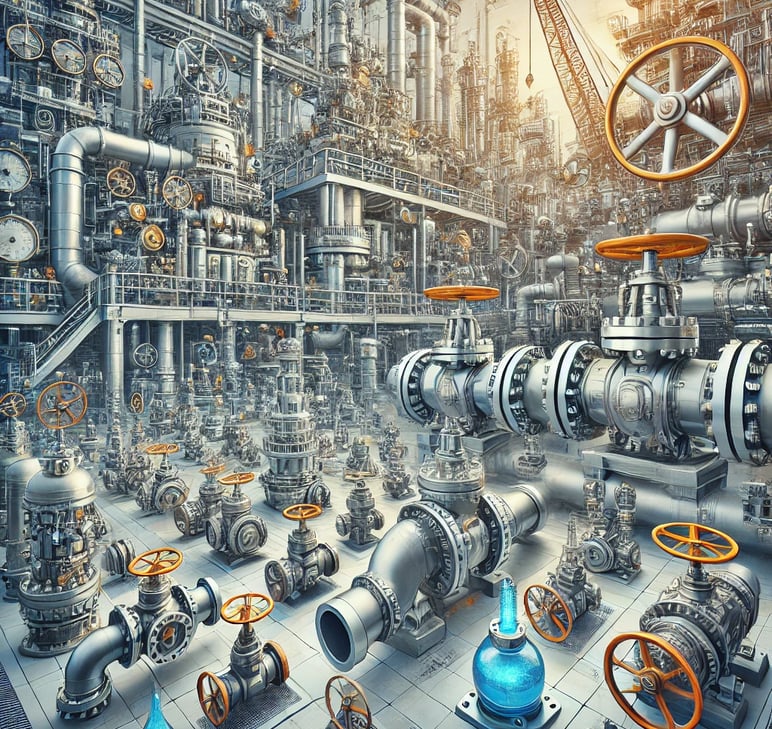
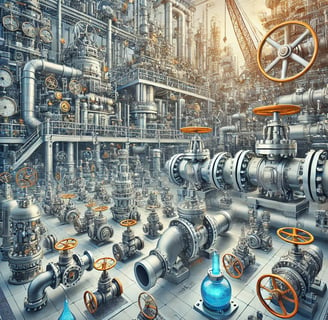
Heat Exchangers & Pressure Vessels – Managing Heat Transfer & Fluid Storage 🌡🔧
Heat exchangers and pressure vessels are critical components in refineries, chemical plants, LNG terminals, and power plants. They regulate temperature, pressure, and energy efficiency in fluid processing and storage operations.
✅ 1. Types of Heat Exchangers & Their Functions 🔄🔥
Heat exchangers transfer heat between fluids while maintaining system efficiency. They are used for cooling, heating, condensing, and evaporation.
1.1 Shell & Tube Heat Exchangers – Common in Refineries & Chemical Plants 🏭⚙
✔ Shell & tube heat exchangers use a bundle of tubes to transfer heat between two fluids.
✔ Suitable for high-pressure and high-temperature processes.
✅ Applications:
Crude oil preheating in refineries.
Steam generation in power plants.
Chemical reaction cooling in petrochemical industries.
🔹 Example: Oil refineries use shell & tube heat exchangers to preheat crude oil before distillation.
1.2 Plate Heat Exchangers – Used in LNG Plants & Cooling Systems ❄♻
✔ Plate heat exchangers use stacked metal plates to transfer heat efficiently.
✔ More compact and efficient than shell & tube heat exchangers.
✅ Applications:
LNG regasification plants (cooling supercooled natural gas).
Chilled water systems in HVAC & data centers.
Food & beverage industry for pasteurization.
🔹 Example: LNG terminals use plate heat exchangers to convert liquefied gas back into vapor for transport.
1.3 Air-Cooled Heat Exchangers – Used Where Water Cooling is Not Possible 🌬💨
✔ Uses ambient air instead of water for cooling, reducing water consumption.
✔ Common in remote locations, arid regions, and offshore platforms.
✅ Applications:
Cooling steam in power plants.
Petrochemical processing.
Refineries in water-scarce areas.
🔹 Example: Desert-based refineries use air-cooled heat exchangers to avoid excessive water use.
1.4 Double Pipe Heat Exchangers – Used for High-Temperature Oil & Gas Processes 🔄🔥
✔ Simple design with one pipe inside another for direct heat transfer.
✔ Used for small-scale, high-temperature applications.
✅ Applications:
Viscous fluid heating in heavy oil processing.
High-pressure gas cooling.
Cryogenic applications in chemical plants.
🔹 Example: Natural gas processing facilities use double pipe exchangers to handle high-pressure gas cooling.
✅ 2. Pressure Vessels & Their Role 🛢⚙
Pressure vessels store and process fluids under high pressure, ensuring safe operation in oil & gas facilities.
2.1 Storage Tanks – For Crude Oil, LNG, and Compressed Gases ⛽🛢
✔ Large aboveground or underground tanks store oil, gas, and chemicals.
✔ Built with reinforced steel and corrosion-resistant coatings.
✅ Applications:
Crude oil & fuel storage at refineries.
LNG storage at -162°C for global transport.
Compressed gas storage (propane, hydrogen, CO₂).
🔹 Example: LNG storage tanks use cryogenic insulation to keep natural gas liquefied.
2.2 Reactors & Separators – Used in Chemical Processing & Refining 🔬🏭
✔ Reactors facilitate chemical reactions under controlled pressure & temperature.
✔ Separators remove gas, oil, and water mixtures in refineries.
✅ Applications:
Catalytic reactors in crude oil refining.
Gas-liquid separators in natural gas processing.
Chemical reactors for fertilizer & plastic manufacturing.
🔹 Example: Petrochemical plants use high-pressure reactors to convert crude oil into gasoline & polymers.
2.3 High-Pressure Boilers – Essential in Power Plants & Steam Generation 🔥♨
✔ Boilers generate steam for power plants & industrial processes.
✔ Operate at high pressures and temperatures.
✅ Applications:
Steam turbines in power plants.
High-pressure steam supply in oil refineries.
Process heating in chemical industries.
🔹 Example: Coal-fired power plants use high-pressure boilers to generate steam for electricity production.
🔍 Why Heat Exchangers & Pressure Vessels Matter in Industry
🔹 Ensures energy efficiency & temperature control in refineries & LNG plants.
🔹 Prevents pressure buildup, reducing explosion risks in pipelines & tanks.
🔹 Optimizes crude oil processing, steam generation, and gas storage.
🚀 These components are essential for safe, efficient fluid processing in global industries! 🌍
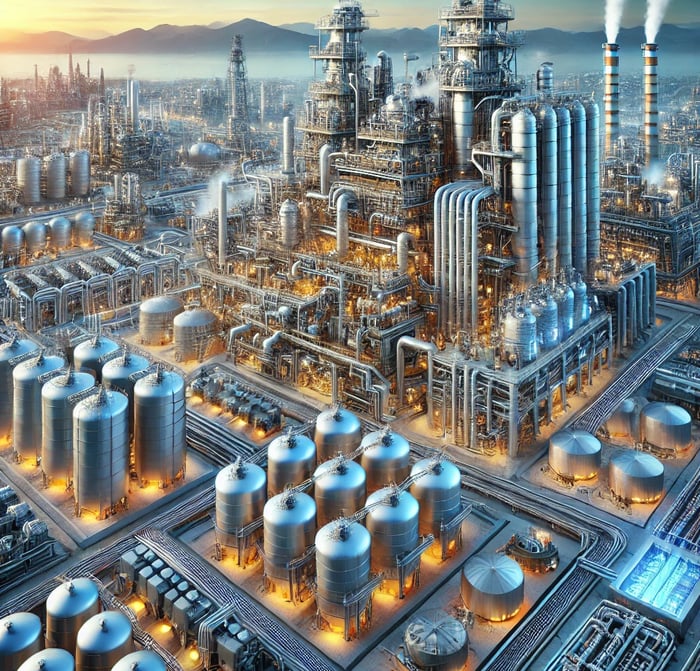
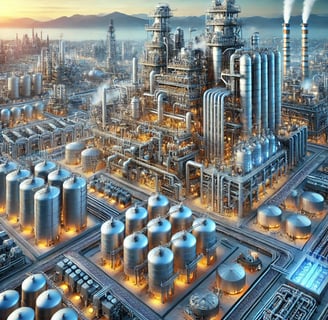
Gaskets, Flanges & Expansion Joints – Strengthening Pipeline Integrity 🔩🔧
Gaskets, flanges, and expansion joints are small but essential components in piping systems. They prevent leaks, absorb vibrations, and accommodate structural movement, ensuring safe and reliable pipeline operations in industries such as oil & gas, power plants, refineries, and chemical processing.
✅ 1. Flanges – Secure Pipeline Connections 🔗🔩
Flanges connect pipes, valves, and equipment by creating a tight, strong, and leak-proof joint.
1.1 Slip-On Flanges – Easy to Install & Cost-Effective 🔄🔧
✔ Slip-on flanges slide over the pipe and are welded into place.
✔ Suitable for low-pressure and non-critical piping systems.
✅ Applications:
Water supply pipelines.
Cooling systems in refineries.
Compressed air & low-pressure steam pipelines.
🔹 Example: Power plants use slip-on flanges in their secondary cooling water systems.
1.2 Weld Neck Flanges – Ideal for High-Pressure & High-Temperature Systems 🔩🔥
✔ Designed for extreme pressure and temperature conditions.
✔ The long neck provides extra strength, reducing stress at the flange joint.
✅ Applications:
High-pressure steam pipelines in power plants.
Crude oil processing units in refineries.
Offshore drilling platforms.
🔹 Example: Refineries use weld neck flanges in high-temperature distillation columns to prevent leaks.
1.3 Blind Flanges – Used to Seal Off Piping Ends for Maintenance 🔧🚧
✔ Blind flanges close off the ends of pipelines or equipment for future expansion or repairs.
✔ Prevents fluid flow and pressure loss when sections of the pipeline are not in use.
✅ Applications:
Shutdown operations in oil & gas facilities.
Pressure testing new pipeline sections.
Sealing off unused ports in chemical plants.
🔹 Example: LNG terminals use blind flanges to temporarily shut down sections of gas pipelines during maintenance.
✅ 2. Gaskets – Ensuring Leak-Proof Joints 🛢🔄
Gaskets create a tight seal between flanges, preventing leaks in high-pressure and high-temperature pipelines.
2.1 Metallic Gaskets – Used in Extreme Pressure & Temperature Conditions 🏭🔥
✔ Made from stainless steel, copper, or aluminum.
✔ Ideal for harsh industrial environments.
✅ Applications:
Refineries & petrochemical plants.
Steam boilers & high-pressure gas lines.
Nuclear power plants.
🔹 Example: Metallic gaskets in nuclear reactors ensure radiation-resistant sealing in high-pressure environments.
2.2 Spiral Wound Gaskets – Common in Oil Refineries & Offshore Rigs 🌊🏗
✔ A combination of metal and filler material for extra durability.
✔ Absorbs vibrations and pressure fluctuations.
✅ Applications:
Oil refineries & offshore drilling rigs.
Cryogenic piping in LNG plants.
High-pressure hydrogen pipelines.
🔹 Example: Spiral wound gaskets in deep-sea oil pipelines prevent fluid leaks under extreme water pressure.
2.3 Rubber & Fiber Gaskets – Used in Water & Low-Pressure Pipelines 💧🛠
✔ Flexible, easy to install, and cost-effective.
✔ Common in municipal water supply and HVAC systems.
✅ Applications:
Potable water & sewage pipelines.
Cooling systems in industrial plants.
Food & beverage processing lines.
🔹 Example: Municipal water treatment plants use rubber gaskets for secure pipe connections in drinking water pipelines.
✅ 3. Expansion Joints – Absorbing Movement & Reducing Stress 🔄⚙
Expansion joints handle thermal expansion, vibrations, and structural shifts in pipelines.
3.1 Metallic Expansion Joints – Handle Thermal Expansion in Steam Lines 🔥♨
✔ Made from stainless steel or Inconel, these joints expand and contract with temperature changes.
✔ Protects pipes from thermal stress and cracking.
✅ Applications:
Steam pipelines in power plants.
Refineries processing high-temperature hydrocarbons.
Aircraft fuel systems.
🔹 Example: Coal-fired power plants use metallic expansion joints to prevent stress fractures in high-pressure steam lines.
3.2 Rubber Expansion Joints – Absorb Vibration in Pumping Stations 🏭🔄
✔ Flexible rubber construction dampens vibrations and absorbs shocks.
✔ Prevents damage from pump and motor movements.
✅ Applications:
Water pumping stations.
Chemical processing units.
HVAC and refrigeration systems.
🔹 Example: Pumping stations in oil terminals use rubber expansion joints to reduce mechanical stress from large fluid pumps.
3.3 Fabric Expansion Joints – Used in High-Temperature Exhaust Ducts 🔬🔥
✔ Made from heat-resistant fabric materials for high-temperature gases.
✔ Used in industrial exhaust and flue gas systems.
✅ Applications:
Gas turbines & jet engine exhaust systems.
Flue gas ducts in power plants.
Waste heat recovery systems.
🔹 Example: Fabric expansion joints in power plants ensure safe exhaust gas flow at temperatures above 1000°C.
🔍 Why Gaskets, Flanges & Expansion Joints Matter in Piping Systems
🔹 Prevents leaks and improves pipeline safety.
🔹 Reduces mechanical stress and extends pipeline lifespan.
🔹 Ensures smooth operations in high-pressure & high-temperature environments.
🚀 These components are crucial for maintaining pipeline integrity across industries! 🌍
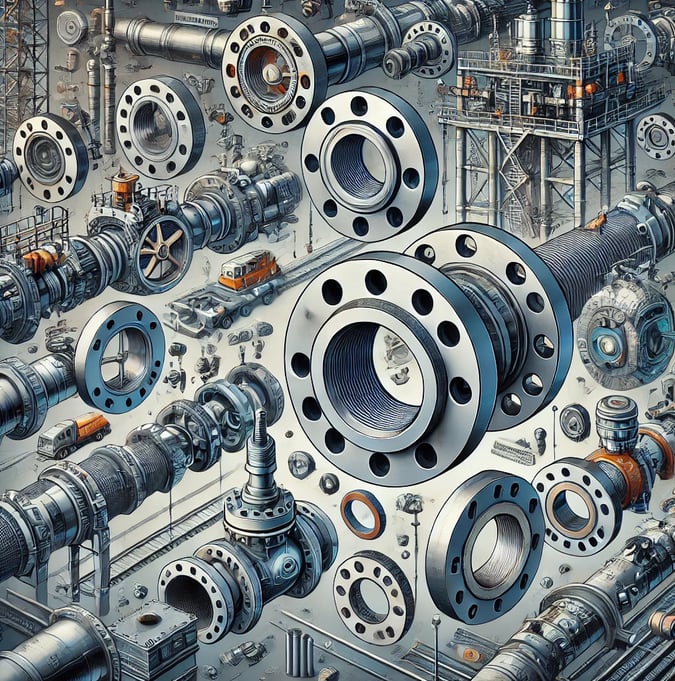
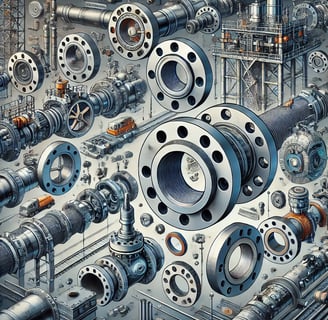
Piping Insulation & Coatings – Preventing Corrosion & Managing Temperature 🌡🛡
Pipelines are constantly exposed to extreme temperatures, moisture, mechanical stress, and corrosive substances. Proper insulation and protective coatings ensure pipeline longevity, operational efficiency, and safety in industries like oil & gas, LNG, chemical processing, and
power generation.
✅ 1. Types of Piping Insulation 🔥❄⚡
Insulation is essential for temperature control, energy efficiency, and equipment protection.
1.1 Cold Insulation – Used in LNG Transport & Cryogenic Piping ❄🌊
✔ Cold insulation prevents ice buildup, condensation, and energy loss.
✔ Required in cryogenic applications where temperatures reach -162°C (LNG transport).
✅ Applications:
Liquefied Natural Gas (LNG) pipelines & storage tanks.
Cryogenic oxygen & nitrogen transport.
Aerospace fuel systems.
🔹 Example: LNG terminals use polyurethane foam insulation to maintain cryogenic temperatures in gas pipelines.
1.2 Thermal Insulation – Prevents Heat Loss in Steam & Hot Oil Pipelines 🔥♨
✔ Reduces heat loss and improves energy efficiency in high-temperature pipelines.
✔ Commonly made of mineral wool, fiberglass, or calcium silicate.
✅ Applications:
Steam pipelines in power plants.
Hot oil transport in refineries.
Chemical reactors with high-temperature processes.
🔹 Example: Refineries insulate steam lines with mineral wool to reduce energy consumption and heat loss.
1.3 Electrical Insulation – Protects Against Static Discharge & Sparking ⚡
✔ Prevents electrical hazards, arcing, and ignition risks in volatile environments.
✔ Used in petroleum storage tanks, fuel pipelines, and explosive atmospheres.
✅ Applications:
Fuel transfer systems in oil terminals.
Electrically conductive pipeline networks.
Aviation fueling systems.
🔹 Example: Oil pipelines use anti-static coatings to prevent electrical discharge in flammable environments.
✅ 2. Corrosion Protection Coatings 🛡💧
Pipeline coatings protect against corrosion, erosion, and environmental degradation.
2.1 Fusion Bonded Epoxy (FBE) Coating – Protects Against Corrosion in Buried Pipelines 🛢🔄
✔ Electrostatically applied epoxy coating that resists corrosion and chemical attacks.
✔ Ideal for underground and underwater pipelines.
✅ Applications:
Oil & gas pipelines in harsh environments.
High-pressure water pipelines.
Seawater desalination plants.
🔹 Example: Trans-Alaska Pipeline uses FBE coatings to prevent corrosion in permafrost conditions.
2.2 Galvanized Coatings – Used in High-Humidity Offshore Structures 🌊🏗
✔ Zinc-coated steel surfaces provide rust resistance in marine environments.
✔ Used for structural components and exposed piping.
✅ Applications:
Offshore oil rigs & drilling platforms.
Shipbuilding & marine pipelines.
Bridges and structural supports in humid climates.
🔹 Example: North Sea oil rigs use galvanized steel coatings to withstand saltwater exposure.
2.3 Internal Pipe Linings – Prevents Fluid Contamination & Erosion 🔬💧
✔ Protects against chemical corrosion, scaling, and internal pipe wear.
✔ Used for drinking water, chemical transport, and food processing.
✅ Applications:
Water distribution networks.
Petroleum and refined product pipelines.
Food-grade liquid transport.
🔹 Example: Oil pipelines use polymer-based linings to reduce friction losses and prevent paraffin buildup.
✅ 3. Case Study: How Coatings Extended the Lifespan of the Keystone Pipeline 🏗📊
The Keystone Pipeline, which transports crude oil from Canada to the U.S., faced corrosion risks due to environmental exposure.
3.1 Used Advanced Epoxy Coatings to Prevent External Corrosion 🛢
✔ Applied dual-layer FBE coatings to resist moisture, soil contaminants, and abrasion.
✔ Reduced corrosion rates by 75% compared to standard coatings.
3.2 Implemented Robotic Coating Inspection Technology 🤖🔍
✔ Deployed AI-powered robotic crawlers to scan for coating defects & cracks.
✔ Automated corrosion detection and repair scheduling.
3.3 Reduced Maintenance Costs by 30% Over the Pipeline's Lifecycle 💰⚙
✔ Lower pipeline downtime & fewer corrosion-related failures.
✔ Improved environmental compliance & sustainability.
🔹 Result: Keystone Pipeline increased operational efficiency and extended its lifespan by 20+ years.
🔍 Why Piping Insulation & Coatings Matter
🔹 Prevents pipeline failures caused by corrosion and thermal stress.
🔹 Improves energy efficiency and safety in high-temperature & cryogenic systems.
🔹 Extends pipeline lifespan, reducing maintenance costs.
🚀 Proper insulation and coatings are essential for long-lasting and reliable pipeline networks! 🌍
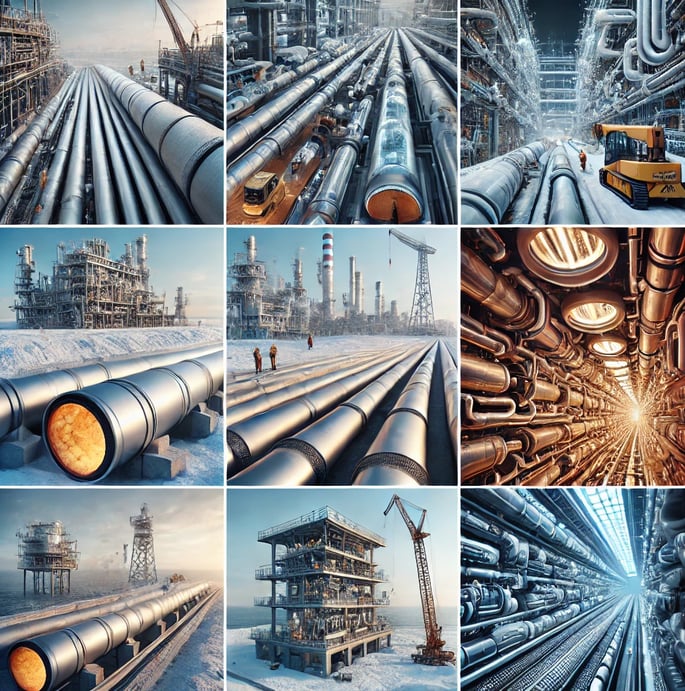
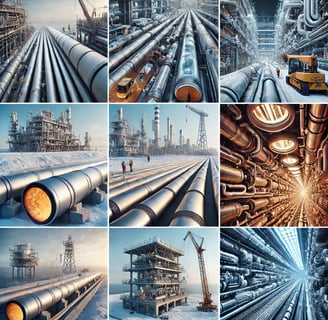
Flow Measurement & Control – Instruments Used in Oil & Gas Plants 🌊⚡
Accurate flow measurement and control are essential for optimizing efficiency, ensuring safety, and improving process control in oil & gas refineries, LNG plants, and chemical processing facilities. Flow meters measure the rate of fluid movement, while control valves regulate flow based on process demands.
✅ 1. Common Flow Meters & Their Applications 🔄📏
Flow meters measure the movement of fluids (liquids, gases, steam) through pipelines, ensuring accurate process control and leak detection.
1.1 Orifice Flow Meters – Used in Gas Processing & Steam Pipelines 🔄💨
✔ Orifice meters use a pressure drop principle to measure flow rate.
✔ Installed in high-pressure gas and steam lines for accurate readings.
✅ Applications:
Steam pipelines in power plants.
Gas processing units in refineries.
Natural gas flow measurement in pipelines.
🔹 Example: Orifice meters in refineries help monitor steam flow in distillation columns.
1.2 Turbine Flow Meters – Ideal for Fuel & Petroleum Flow Measurement ⚙⛽
✔ Turbine meters measure flow by detecting the rotation speed of an internal turbine.
✔ Highly accurate for liquid fuel measurement.
✅ Applications:
Petroleum fuel transport pipelines.
Jet fuel distribution in airports.
LNG and crude oil metering stations.
🔹 Example: Oil tankers use turbine meters to accurately track fuel transfer volumes.
1.3 Ultrasonic Flow Meters – Non-Invasive & Highly Accurate for Crude Oil Transport 💡📡
✔ Uses sound waves to measure fluid velocity without direct pipe contact.
✔ No pressure loss or risk of leaks since they are clamped externally.
✅ Applications:
Crude oil pipelines in refineries.
LNG plants and gas processing units.
Water treatment & desalination plants.
🔹 Example: Ultrasonic flow meters in oil pipelines provide real-time flow data without disrupting operations.
1.4 Coriolis Flow Meters – Used for Mass Flow Measurement in LNG Plants 🚀🛢
✔ Measures mass flow based on fluid inertia (Coriolis effect).
✔ Ideal for high-accuracy measurement of high-viscosity and cryogenic liquids.
✅ Applications:
LNG (Liquefied Natural Gas) flow measurement.
Heavy crude oil transport.
Chemical & pharmaceutical industries.
🔹 Example: LNG terminals use Coriolis meters to monitor precise gas-to-liquid flow rates.
✅ 2. Flow Control Valves 🚀🔄
Flow control valves regulate fluid movement and pressure in piping systems.
2.1 Globe Control Valves – Regulate Precise Fluid Flow in Refineries 🌊⚙
✔ Provides smooth flow modulation by adjusting the valve opening.
✔ Used for precise fluid flow control in high-pressure applications.
✅ Applications:
Oil refining & petrochemical plants.
Boiler feedwater & cooling systems.
Steam control in power plants.
🔹 Example: Globe valves regulate cooling water flow in LNG processing units.
2.2 Butterfly Valves – Used for Large-Volume Flow Control 🔄💨
✔ Quick shut-off & control of high-flow pipelines.
✔ Requires less space and is lightweight.
✅ Applications:
Water & wastewater treatment plants.
Crude oil and natural gas pipelines.
Cooling towers & air handling units.
🔹 Example: Oil refineries use butterfly valves in large pipelines to optimize fluid movement.
2.3 Automated Smart Valves – Integrated with AI & IoT for Remote Monitoring 💡🔧
✔ Uses AI and IoT sensors for real-time remote control.
✔ Improves pipeline efficiency and leak detection.
✅ Applications:
Automated refinery control systems.
Gas pipeline pressure regulation.
Offshore oil platforms & remote monitoring stations.
🔹 Example: Shell uses AI-powered smart valves to monitor real-time flow data and adjust valve settings remotely.
🔍 Why Flow Measurement & Control Matter in Oil & Gas
🔹 Ensures accurate metering of fuel, crude oil, and natural gas.
🔹 Prevents overpressure and system failures in pipelines.
🔹 Reduces waste and enhances process efficiency.
🚀 Accurate flow measurement and smart control systems are crucial for optimizing oil & gas operations! 🌍
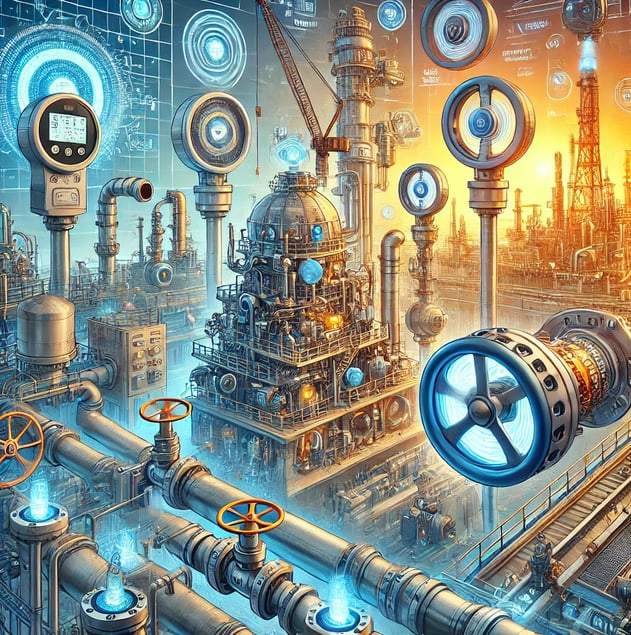
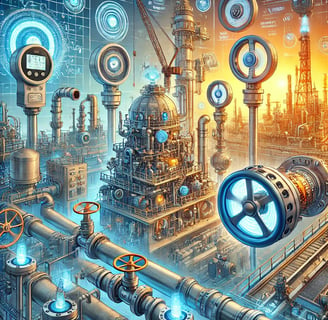